High-Speed VMCs are suited for mold industry.
Press Release Summary:
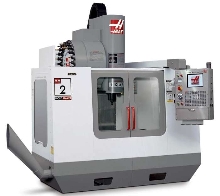
Featuring cast-iron construction, VM-2 incorporates linear guides on all axes, brushless servos, fine-pitch ballscrews, and digital encoders. It uses 12,000-rpm, 40-taper, inline direct-drive spindle powered by 30 hp vector dual drive system. With max weight capacity of 3,000 lb, 36 x 18 in. table features T-slots in vertical and horizontal directions. Features include 30 x 20 x 20 in. work cube, 24+1 side-mount tool changer, and machining software with look-ahead.
Original Press Release:
Haas Expands Line of High-Speed VMCs for Mold Makers
Following on the success of its VM-3, Haas Automation, Inc., expands its new line of VMCs designed for the mold industry. The company's latest entry is the VM-2, a high-performance machine with a 30"x20"x20" work cube, a 36"x18" table, a 12,000-rpm inline direct-drive spindle and a high-speed control with full look-ahead.
Like all Haas VMCs, the VM-2 features massive cast-iron construction. Extensive internal ribbing on the castings increases rigidity and damps vibrations. High-precision linear guides on all axes further increase rigidity and stiffness, while providing a low coefficient of friction and long-term reliability. High-speed brushless servos, combined with fine-pitch ballscrews and high-resolution digital encoders, ensure ultra-precise positioning and extreme repeatability.
The VM-2 is equipped with a 12,000-rpm, 40-taper spindle that uses a unique inline, direct-drive system that couples the motor directly to the spindle rather than using belts (a major source of heat). This results in less vibration, less heat and less noise than other drive systems, providing excellent surface finishes, extreme thermal stability and quiet operation. Powered by a 30-hp vector dual drive system, the spindle produces plenty of low-end torque, as well as the speed necessary for high-speed machining. On-the-fly wye-delta switching provides a wide constant horsepower band.
To ensure thermal stability, coolant is circulated through a jacket in the VM-2's head casting to remove heat generated by the spindle. The headstock is also lined with insulating material to prevent radiated heat from affecting the casting, and air is circulated through the entire assembly for additional cooling. An electronic thermal compensation algorithm in the Haas control accurately models ballscrew heating from high duty cycles and automatically corrects for any expansion that could cause positioning errors.
For maximum fixturing versatility, the VM-2's unique 36"x18" cast-iron table features standard T-slots in both vertical and horizontal directions, as well as precision dowel-pin bores and an array of drilled and tapped holes. It has a maximum weight capacity of 3,000 lb.
The VM-2 comes standard with a side-mount tool changer that holds 24 tools plus one in the spindle; it features a quick-change double-arm gripper that swaps tools in 2.8 seconds. Also standard are an automatic chip auger system, remote jog handle, automatic air gun, high-speed machining software with look-ahead, hard drive with Ethernet interface, floppy drive, Visual Quick Code programming, user-definable macros, coordinate rotation & scaling and spindle orientation.
Available options include a 30k spindle, linear scales, Visual Quick Code probing and expanded program memory (up to 16 MB).