Flow Conditioner eliminates asymmetrical flow profiles.
Share:
Press Release Summary:
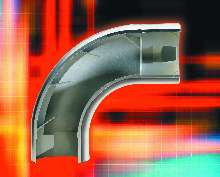
VOREL(TM) 90° Elbow Flow Conditioner optimizes pump performance by eliminating flow anomalies such as process media swirl associated with unconditioned, standard elbows. Flow stream enters pump in uniform and equally distributed pattern. Anti-swirl and inclined vortex-generating profile correction tabs, projecting from inside pipe surface, generate vortices that accelerate and amplify natural pipe effects to create uniform, non-swirling, symmetrical flow profile.
Original Press Release:
VOREL(TM) 90-Degree Elbow Flow Conditioners Increase Pump Performance, Reduce Pump Maintenance and Extend Life
Eliminates Process Media Swirl and Asymmetrical Flow Profiles
San Marcos, CA-March 29, 2003--VOREL 90-Degree Elbow Flow Conditioners from the Vortab Company increase pump performance and reduce pump maintenance by eliminating cavitation and improving flow profiles leading into pumps, which reduces pump repair costs and extends pump life to cut overall operating costs. No added space is taken up in installation as VOREL replaces the last remaining upstream elbow in the line.
Pipeline elbows located upstream from pumps create undesirable process media swirl and other asymmetrical flow conditions that damage pumps. The inertia caused by the pipeline elbow shifts the process media to one side of the pipe before it enters the pump, resulting in severe suction recirculation, excessive bearing wear, erosion, noise, and increased maintenance cost. Furthermore, as these uneven flow profiles continue they hit the pump's impeller with high flows on one side and create cavitation on the other side.
To solve this problem, the patented VOREL 90-Degree Elbow is an advanced flow conditioner with a superior tab flow conditioner array that eliminates the flow anomalies associated with unconditioned, standard elbows. A VOREL conditioned flow stream enters the pump in a uniform and equally distributed pattern that results in increased pump bearing life with decreased noise and cavitation and improved pump performance efficiency. In addition, VOREL conditioners isolate and condition out any flow irregularities that may be introduced upstream from the elbow.
Flow disturbances not only affect pump performance, but also adversely affect the accuracy and repeatability of flow measurement and control instrumentation, including differential pressure, turbine, vortex shedding, ultrasonic, thermal and magnetic flowmeter technologies. In today's demanding plant environment, VOREL Elbow Flow Conditioners will ensure flow instrumentation accuracy and repeatability performance for tighter and highly repeatable process control.
VOREL was developed using the same tab-type flow conditioning technology as Vortab's straight run pipe Flow Conditioners, which have been laboratory proven and successfully installed in hundreds of plants worldwide. VOREL's anti-swirl and inclined vortex generating profile correction tabs, projecting from the inside pipe surface, generate vortices that accelerate and amplify these natural pipe effects to create a uniform, non swirling, symmetrical flow profile in a much shorter section of pipe.
The simple, flexible designs of the new VOREL Elbow and VORTAB Insert Sleeve, Short Run, Meter Run and Field Kit flow conditioners provide cost effective solutions to problematic installations for pumps, flow meters and other process equipment. VOREL and VORTAB provide the most effective flow disturbance isolation, lowest pressure drops and least affect by fouling of any of the flow conditioner technologies on the market today.
VOREL and VORTAB flow conditioners can be made from carbon steel, 316 stainless steel or Hastelloy C-276. Several process connections are available--ANSI flanges, male NPT threads, butt welded preps or retaining wafers. Delivery time is available in less than four weeks, depending on size. Custom configurations are also available from the factory with lead times of 6 weeks or less.
The Vortab Company is a global supplier committed to meeting the needs of its customers through innovative solutions to the most challenging requirements for optimizing the performance of process equipment in gasses or liquids.