Drill Grinding Machine handles point and split point jobs.
Press Release Summary:
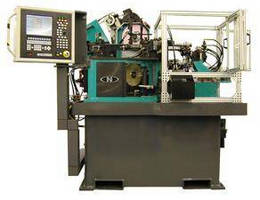
With point geometry and sizing under NC, PS52 offers 3 parallel operations with load/unload simultaneous to point and split grinding. System accommodates multiple part-program storage and can produce drills from 1/16-½ in. to max overall length of 6 ½ in. Production capabilities also extend to point included angles from 80° to 140°; Conventional Point, Helical Point, and Multi-facet point geometries; as well as DIN style A/C/B with split point.
Original Press Release:
Announcing Normac's New PS52 Automatic Drill Point and Split Drill Grinding Machine
Normac's PS52 Drill Point and Split Point Grinder produces:
Drills from 1/16" to 1/2" (1.5 mm to 13.0 mm) to a maximum overall length of 6-1/2"
Point included angles from 80 to 140 degrees.
Rake angles up to 20 degrees.
Lip relief angle up to 24 degrees.
Conventional (Seller's) Point, Helical Point and Multi-facet point geometries.
DIN style "A", "C", and "B" (Sometimes referred to as Type "U" and Type "S" points) with split point up to 20 degrees rake angle.
Approximately 10 second cycle time for 1/2" (13.0 mm) drills.
Features:
Point geometry and sizing under numerical control.
3 parallel operations with Load /Unload simultaneous to the point and split grinding operation.
User-Friendly CNC with part geometry programs created by data input.
Multiple part-program storage.
Can also be set to grind either drill point OR split grind only.
Fast Setup.
Off-line collet & cartridge assembly setup.
Drill is clamped one time for all grinding operations insuring point orientation and accuracy.
All cartridge assemblies are precision keyed for accurate loading.
CAN BE USED IN NEW TOOL PRODUCTION GRINDING OR IN DRILL RE-POINTING AND REFURBISHING.
Basic Cycle Description:
Station #1 Transfer and Locator: A fluted drill blank is loaded from a Normac Hopper style loader (removable for robotic loading), via a push rod and vee-block, similar to Normac C500 loaders.
The loader pushes the previously finished tool out through the collet and cartridge assembly and into a catch pan.
It then inserts a new tool in the collet and returns to the load position. The collet and cartridge assembly (now loaded) slowly rotate to locate the existing cutting edge for orientation of the drill point. The cartridge transfer assembly then retracts and indexes to insert cartridge assemblies into the grinding stations (#2 and #3).
Station #2 Point Grind: The drill is radially oriented and then point ground at this station. The point geometry is achieved by a combination of drill blank rotation, the side-to-side oscillation of the drill, and in-and-out movement of the grinding wheel. When the point grind is complete, the cartridge assembly is then retracted and indexed by the cartridge transfer assembly, and inserted into the split grind operation. The 10 inch grinding wheel of Station #2 is driven by a 2 HP motorized spindle and contoured by the 2-axis CNC movement of a 4 inch diamond profiling disk.
Station #3 Split Point Grind: The drill is again radially oriented and the plunge grind at this station completes the split point geometry. When the split grind is finished, the cartridge assembly with the completed drill is then removed and the cartridge transfer assembly again indexes to deposit the finished tool back in Station #1 to repeat the cycle. The 12 inch grinding wheel of Station #3 is driven by a 5 HP motor and belt driven spindle and is plunge-dressed using a 2-3/4" formed diamond dressing roll.
To run your test tooling or to schedule a visit to see the PS52, call or e-mail:
Jerry Martin: jlmartin@normac.com
Sam Huntley: huntley@normac.com
Ray Bodie: rayb@normac.com
Contact Normac today for further information.