Thermal Simulation Dramatically Reduces Time to Design Complex Burn-in Test System
Share:
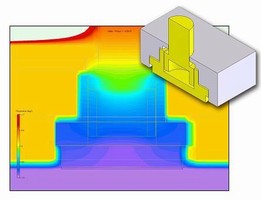
(January 15, 2008) - Antares Advanced Test Technologies used Flomerics' Flotherm thermal simulation software to develop a new burn-in test system for electronic components in one-third the amount of time that would have been required using conventional design methods. The design of the test system was challenging because of the need to maintain low thermal resistance between the heating and cooling systems and the device under test while compensating for variations in device height. "By using thermal simulation to evaluate a considerable number of design alternatives without building prototypes we were able to develop a design that met all of the customer's requirements in only two and a half weeks," said Trevor Moody, Thermal and Mechanical Engineer for Antares, based in Phoenix, Arizona.
An Antares customer that produces semiconductors for military and space applications recently asked Antares to provide a burn-in test system that could simultaneously handle a wide range of products. In order to handle these products, each socket would need to be capable of sensing the temperature of the device, and either heating or cooling the device to keep it at the proper burn-in temperature which may be either above or below ambient temperature. The devices have small variations in their packaging that can cause them to vary up to 0.015 inch in height and also may cause them to tilt at different angles. The mechanical socket assembly must accommodate this range of movement while maintaining mechanical integrity and providing a highly efficient thermal path between the heating and cooling systems and the device.
"We selected Flomerics' Flotherm thermal simulation software because it is easy to use and can simulate nearly any type of test system," Moody said. "Another advantage of Flotherm is that most of our customers use it for thermal simulation, so they have confidence in our simulation results and we can share models with them."
Thermal simulation enabled Moody to accurately predict the thermal resistance of each design iteration without having to build and test the prototype. The ability to quickly simulate thermal performance made it possible to evaluate a large number of very different design concepts. Thermal simulation also provides much more comprehensive results than physical testing because it predicts temperature at every point in the design. "I could easily identify thermal blockages by looking for changes in temperature across a relatively small area," Moody said. "So I was able to concentrate on reducing thermal resistance in these areas."
Moody was able to complete the most critical portion of the design, creating a mechanism that meets the mechanical and thermal requirements, in only about one-third of the time that would have been required using conventional built-and test design methods. The new test system has already met all performance objectives by enabling the customer to test several types of devices simultaneously at a wide range of temperatures both above and below ambient.
For more information about Flotherm, visit Flomerics' Web site at www.flomerics.com
A high-resolution version of this image is available for download at: flomerics.com/news/gallery/
Flomerics Inc.
US Headquarters
4 Mount Royal Ave., Suite 450
Marlborough, MA 01752
Tel: +1 (508) 357 2012
Fax: +1 (508) 357 2013
E-mail: info@flomerics.com
Web site: www.flomerics.com
FLOMERICS LIMITED
81 Bridge Road o Hampton Court
Surrey KT8 9HH o England
Tel: +44 (0) 20 8487 3000
E-Mail: info@flomerics.co.uk
Website: www.flomerics.com