Wear Plate has non-stick, impact-tolerant surface.
Share:
Press Release Summary:
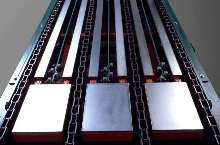
Original Press Release:
Introducing CRODON® Wear Plate, a Revolutionary Advance in Wear Plate Performance
CLEVELAND, OH- Chromium Corporation, one of the most experienced and advanced surface technology companies in the country, introduces CRODON® Wear Plate, a more cost-effective and durable alternative to traditional high-alumina ceramic and abrasion-resistant (AR) wear plates.
CRODON Wear Plate is created through a proprietary process that applies a dense, highly-adherent layer of abrasive and impact-resistant material to the surface of ferrous-based materials. It is made up of the extremely durable CRODON wear surface, a proprietary finish and a steel base metal. CRODON Wear Plate can be fabricated into sheets, strips or rolled on the inner or outer diameter to unique dimensions as tight as 6" on the radius. CRODON Wear Plate is ideal for use in abrasive production environments such as coal handling, mining, lumber mills, sand and gravel, cement manufacturing or any harsh environment where abrasion leads to quick equipment deterioration.
Its unique nonstick, impact-tolerant and abrasion-resistant surface gives CRODON Wear Plate the flexibility to be used in a wide range of applications - chutes, bang boards, flop gates, loading buckets, conveyors, silos, cones, skirt boards and much more.
Wes Busby, operations manager for Smith's Concrete in Nashville, Arkansas, says that CRODON Wear Plate outlasts everything else he has tried on chutes and turrets.
"I love it, he says, "We've got over a year with no wear in places where our other materials wore out in three to six months."
CRODON Wear Plate can last four to six times longer than traditional, through-hardened AR400 steel. In tests performed at a major Texas power plant, CRODON Wear Plate was compared to an AR400 wear plate acting as a bang board for lignite coal prior to entering the crusher. Prior to installation of the test plate, the maintenance manager reported a standard life cycle of six to nine months under normal use. Using a standard ½" thick piece of mild carbon steel with .020" of CRODON wear surface, the test CRODON Wear Plate lasted over 20 months, more than doubling the bang board's life cycle.
The nonstick surface gives CRODON Wear Plate an advantage in sticky situations. Asphalt, wet coal fines, cement and similar materials do not adhere to the surface, and the extremely low coefficient of friction reduces sliding wear.
CRODON Wear Plate's ability to be formed and cut gives it multiple size and shape options, making installation easy. A single sheet of CRODON Wear Plate can replace several pieces needed for the same space outfitted with industrial ceramic tiles. CRODON Wear Plate can be welded, studded and bolted for quick replacement during maintenance, saving precious time and dollars.
"CRODON Wear Plates have saved us a lot of headaches," says Jimmy Harper, production manager for Texas-based Elk Premium Building Products, a leading manufacturer of asphalt roofing shingles. "We've gotten up to seven times the life we used to get from ceramic tiles, and installation is a whole lot easier."
Several Elk facilities successfully use CRODON Wear Plate in granule chutes, fife paddles, T-bars, high-lugs, timing tables and other locations. It has dramatically reduced wear as well as asphalt buildup on production surfaces. In addition to Elk manufacturing facilities, CRODON Wear Plate has been installed in over 25 other asphalt roofing shingle plants.
CRODON Wear Plate is available in four grades used for various application environments including Standard CRODON, CRODON Plus, CRODON Premier and CRODON Advantage. Founded in 1926, Chromium Corporation provides products and services for bulk material handling and general manufacturing and remains the leader in the field of plating and finishing reciprocating engine components. For more information on the CRODON Wear Plate and other products and services, visit the company's web site at www.chromcorp.com or call 1-800-FINISHS.
All trademarks, ®, are registered trademarks of Chromium Corporation. Chromium Corporation is a subsidiary of ElkCorp (NYSE: ELK).