Strand Pelletizer stops cross-contamination.
Press Release Summary:
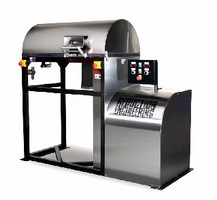
To safeguard against contamination of compounds by stray pellets, Reduction(TM) 800 Series features rounded hood with smooth inner lining of sound-dampening material. Deck has hard-coat anodized aluminum surface that eliminates pellet hang-ups. Usable with any type of pellet classifier or gaylord packaging, machine has one motor drive for upper and lower strand-infeed rollers and another for cutting rotor. Ratio between speeds is adjustable to control pellet size and throughput.
Original Press Release:
First Strand Pelletizer in New Reduction(TM) Range Stops Cross-Contamination and is Easy to Deploy and Operate
KENT, OH, U.S.A., September 20, 2006: A strand pelletizer of completely new design provides safeguards against contamination of compound by stray pellets from previous production runs, makes string-up (manual loading) of strands simpler and faster than with conventional equipment, and enables compounders to use virtually any downstream equipment to take away or package pellets, it was announced today by Reduction Engineering, Inc.
The new Reduction (TM) 800 Series pelletizer is the first system introduced by Reduction Engineering since it purchased the pelletizer product line of Conair in May, after several years of assembling, servicing, and marketing pelletizers for Conair. The design innovations made by Reduction Engineering are particularly valuable for custom compounders, who may make anywhere from two to twelve job changes a day, according to sales manager Chris Case.
"Over the years, Reduction Engineering gathered real-world, shop-floor input from the compounders we worked with and now has developed a pelletizer that addresses the issues that they face every day," said Case. "Most important among the improvements in our 800 Series pelletizer is a solution to the problem of color cross-contamination, which can render an entire order useless to a compounder's customer, cost the compounder considerable effort and expense to make good on the mistake, and result in permanent loss of business."
Even the tiniest cross-contamination (by a few black pellets, for example, in a gaylord-full of beige compound) can yield molded or extruded products with obvious defects, Case pointed out. "In designing the Reduction 800 Series pelletizer, we eliminated the hang-ups and hiding places in conventional equipment that cause stray pellets to find their way into the discharge stream for the next production run," Case said.
For example, the sound-dampening hood covering many pelletizers is a rectangular component that traps pellets in corners and ledges and in the perforations of the interior plates. In contrast, the new Reduction pelletizer has a rounded hood with a pellet-free internal design that includes slots for pellets to fall onto the deck, or isolation plate, on which the working components of the pelletizer are mounted; from there they are easily removed. The inside of the hood has a smooth inner lining consisting of an advanced sound-dampening material. The deck itself has a hard-coat anodized aluminum surface that is easy to clean and has also been designed to eliminate pellet hang-ups, particularly in the area around the opening for the pellet discharge chute, which is flush-mounted to the under-side of the deck.
Case cited three other major innovations in the Reduction 800 Series design:
o Universally adaptable discharge portion. The new pelletizer is the first on the market that can be used with any type of pellet classifier or gaylord packaging, according to Case. "This universal deployment enables compounders to do more with less equipment and increases their versatility in moving frequently from one production run to the next," he said.
The reason for this versatility is that Reduction Engineering has created a large clear space beneath the pelletizer where downstream equipment can be implemented. Instead of placing the motor underneath, as in conventional pelletizers, company designers moved the motor and placed the pelletizer atop a five-foot (1.52 m) table.
"To accommodate differing types of downstream equipment, conventional pelletizers either had a large discharge chute sticking way out from the machine or had to be custom designed," said Case. "Now you can literally 'parallel-park' a gaylord next to the pelletizer one day and the next day replace that gaylord with a pellet classifier, without any modification to our machine."
o Easily targeted infeed portion. To simplify the manual feeding of strands into the pelletizer, Reduction Engineering created a large rectangular funnel outside the entry port, creating an easy target for the strands. While this design has no counterparts in the industry, the infeed still meets standard OSHA safety requirements specifying opening size versus length, according to Case.
o Separate motor drives with 'drop-in' gear boxes. The Reduction 800 Series pelletizer has one motor drive for the upper and lower strand-infeed rollers and another for the cutting rotor. The ratio between the speeds of the two systems is adjustable to provide control over pellet size and throughput. "The gear boxes are custom-made for Reduction Engineering and are simple replacement parts," Case said.
Among other improvements is the use of abrasion-resistant anodized aluminum for many surfaces that come in contact with strands or pellets.
REDUCTION ENGINEERING, INC. is a worldwide supplier of pelletizers, pulverizers, and rotational molding equipment, and it also engineers and commissions turnkey production systems. Founded in 1994 as a builder of pulverizers for converting pellets to powders, the company began machining rotor knives for Conair pelletizers in 2000, took over assembly of the pelletizers in 2002, and purchased the line from Conair in 2006. Rotational molding equipment manufacture is carried on by a Brazilian affiliate, ROTOLINE INDUSTRIAL EQUIPMENT LTDA, for which Reduction Engineering operates a sales office and service center in Kent, OH, U.S.A.
Reduction Engineering, Inc. is headquartered at 4430 Crystal Parkway, Kent, OH 44240 U.S.A. Tel: 1-330-677-2225. Fax: 1-330-677-4048. Email: sales@reductionengineering.com. Visit www.reductionengineering.com.