Software Suite combines 5 physical design components.
Share:
Press Release Summary:
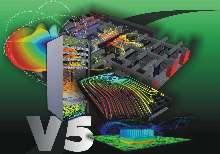
Flomerics software addresses different aspects of physical design of electronics in one analysis environment, eliminating communications barriers between different people involved in same process. It consists of Flo/PCB for conceptual thermal design of PCBs, FloTHERM for system-level thermal design and optimization of electronics systems, Flo/EMC for electromagnetic compatibility simulation, and Flo/STRESS for predicting thermomechanical stresses.
Original Press Release:
Flomerics' Version5 Software is First to Integrate Physical Design in One Environment
(August 18, 2004) -- Flomerics has introduced a new suite of software products that is the first to integrate the major contributors to the physical design of electronics in a single analysis environment. The Flomerics Version5 integrated suite consists of Flo/PCB for conceptual thermal design of printed circuit boards, FloTHERM for system-level thermal design and optimization of electronics systems, Flo/EMC for electromagnetic compatibility (EMC) simulation, and Flo/STRESS for predicting thermomechanical stresses. The new suite dramatically reduces design leadtime by addressing many different aspects of physical design in a single analysis environment, and eliminating communications barriers between the different people involved in the process.
"Using a single environment for thermal and EMC analysis helped us bring a new ruggedized computer to market 20% faster by providing performance information prior to the prototype stage that helped us optimize the tradeoff between cooling management and EMC," said Jean Philippe Tigneres, Environmental Group Manager for Barcoview, Toulouse, France.
The new integrated design process enabled by the suite typically begins when the systems architect develops the initial concept design by creating a functional block diagram in Flomerics' Flo/PCB software. Hardware design engineers can then derive the first physical layout directly from the block diagram. A powerful 3D computational fluid dynamics solver predicts airflow and temperature, for both sides of the board, in minutes. Cooling management can thus be considered from the earliest stages of the design process. Changes made to the functional block diagram are instantly reflected in the physical layout and thermal representations. This keeps all team members in sync and enables them to contribute to concept development in real time.
As mechanical engineers begin to develop the physical design, they can drag the Flo/PCB model and drop it into a system level thermal design that they develop with Flotherm software. The integrated environment not only ensures the transmittal of accurate information to mechanical engineers but also provides immediate notification of design changes. The result is that mechanical engineers can identify thermal issues in the early stages of the design process, long before prototypes are available, and perform design studies to resolve them.
The same model that is created for system level thermal analysis can also be used to address EMC issues far earlier than is normally possible. A step-by-step approach to EMC analysis enables generalist mechanical engineers to optimize the shielding effectiveness of their enclosures with little additional effort and without calling in an EMC specialist. Being able to address thermal management and EMC issues within a single environment makes it possible for mechanical engineers to get a head start on the difficult design tradeoffs that are frequently required between these two disciplines.
The design of the Barcoview ruggedized computer provides a good example of how this process can work in the real world. Long before prototypes were built, Tigneres resolved thermal issues by increasing the size of the inlet and outlet grilles on the panel of the computer. Then, instead of waiting for physical tests to see if this caused EMC problems, he analyzed the system with Flo/EMC and used the information he gained to reshape the openings to reduce emissions to acceptable levels.
Flomerics' new integrated analysis environment is supported by www.SmartParts3D.com - an extensive web-based library of ready-to-run models for common parts such as fans, heat sinks, IC packages and standard enclosures, which further reduces the engineering time required for creating simulations.
For more information, visit Flomerics' Web site at www.flomerics.com