Molder Saves Significant Energy Costs with Move to Desiccant Drying System
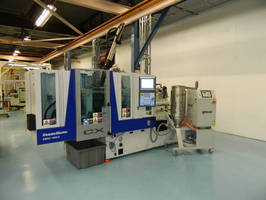
Sinicon Plastics, a world - class custom Injection Molder was founded in 1968 in Pittsfield Massachusetts. Sinicon Plastics specializes in molding engineering resins and liquid silicone for medical, military, aerospace and industrial applications. They offer horizontal/vertical insert molding, micromolding, cleanroon molding, overmolding, secondary machining, assembly and in-house tool building. Production volumes range from prototype to 100,000's of parts.
They have a dedicated staff, many with over 20 years in the industry, with a focus on providing superior customer service and successfully taking on the most demanding of projects.
In 2010 the company relocated to a newer and larger facility in Dalton, MA (located next to Pittsfield) that more than doubled their space. They renovated the 35,000 square foot building and created a state of the art molding facility that now includes in-house tool building.
The move provided the opportunity for the company to investigate energy savings initiatives and ways to reduce their energy consumption. Focusing on two key areas, resin drying and factory lighting, the company has taken significant measures that have allowed them to keep their electric costs in the new building equal to that of their previous smaller space.
"After we purchased all new energy efficient dryers from Dri-Air and retrofitted more efficient lighting we haven't seen any increase in our electric bill - although we have doubled in size in our new space," said David Allen, President of Sinicon.
With this move to the new facility, Sinicon Plastics implemented a more energy efficient plastic drying system using today's latest drying technology from Dri-Air Industries. "Resin drying is a major component of our energy costs," adds Allen. "We had a few Dri-Air dryers in house and had been very happy with their performance. But when Dri-Air came to our plant and performed an energy audit for us - showing the benefits of fully converting to their drying systems - it was an easy decision to switch over completely our drying capabilities. The Dri-Air systems have saved us significantly with our energy costs, has improved the quality of resin drying, and reduced the labor associated with our resin drying function."
New Dri-Air Drying System Uses Half the Energy Of Tray Ovens
Sinicon previously used tray ovens for all their resin drying - with three 10-tray units equipped with timers. The process used to dry material consisted of placing the un-dried material on trays in the ovens where heated ambient air bakes the moisture out of the material. This process takes a considerable amount of time as the ambient air is not dried, nor is the air circulated through the oven - it is more of a convection process than the circulation of the air through the material. Other factors that resulted in extended drying times included the use of solid trays where the air cannot circulate through the material, and the inability to have different temperatures in the oven for different materials. Additionally, labor is required to move the resin from the oven trays to the molding machines. Moving these resins within the trays can lead to contamination issues where one type of resin falls into another - which causes rejects and increases costs.
"The new dryers supplied by Dri-Air use half the amount of energy compared to the tray ovens. With these ovens we were forced to dry different resins all at the same temperature. We would leave the resin in them overnight to dry so that by morning we had resin suitable for production," said Mr. Allen. "We found with the Dri-Air desiccant bed dryers we cut countless hours of drying out of our process. It dried the resin faster and better and we can customize the drying parameters to accommodate the resin it is drying. The portable dryers also included conveying equipment that moves the resin right into the small receivers on the press - eliminating the need to us to manually move it. The timers allow us to start drying the resin late at night so that each morning we are ready for production."
Net results of the ovens inefficiency translates to:
o Drying times that are 12 - 24 times longer than required (Requiring the ovens to run 24 hours a day)
o As each oven can only run one temperature, all three ovens are operating 24 hours a day to accommodate resins with different drying temperatures, regardless if the oven is full or not.
oInconsistently dried material as wet, ambient air, in lieu of circulated, dry air is used to dry material leading to bad parts, longer production runs.
Sinicon's new drying system consists of individual portable desiccant dryers that enable them to dry material at the correct drying temperature for fast, efficient drying using desiccated (dry) air. This air is forced through the resin through the use of a blower, with the heated, dry air dispersed through the material by a properly designed hopper that holds the material. These dryers also convey the material directly to the press, eliminating the need for any additional labor to transport the resin and any contamination from moisture.
Dri-Air dryer efficiencies include:
o 50% reduction in energy consumption
o Faster drying times, 2 hours vs. 12 (less on time)
o Ability to dry small quantities of resins efficiently
o Properly dried material = less scrap = shorter production runs = less electricity
o Ability to dry material at its correct drying temperature
o Automatic timers for starting and stopping prior to and during production
o Convey dried material directly to the press - keeps the resin dry while eliminating hand loading.
o Multiple, smaller dryers can be turned on / off as needed - in lieu of running three larger ovens continuously.
o Usage monitors: Dryers will lower drying temperatures automatically when usage slows or stops, reducing energy consumption.
o On demand regeneration - Dryers will automatically adjust regeneration times (the time required to remove the moisture in the dryer) based on usage, moisture in the resin and ambient conditions.
Taking Advantage of Energy Program Rebates
Sinicon Plastics also received a check that subsidized 50% of their dryer purchase from the Western MA Electric Company in the amount of $30,000. "This funding comes from the conservation surcharge that the energy companies use to fund the promotion of energy consumption savings measures. It's a fantastic program and we were glad to be able to take advantage of it," said Mr. Allen.
Bob Dvorchik, the Supervisor of Commercial & Industrial Energy Conservation Programs at WMECO, located in Pittsfield, MA adds, "This program offers companies in Western MA an incredible opportunity to examine and reduce their energy consumption by significantly reducing the cost of implementing new energy savings measures. When companies examine their ROI on energy savings investments such as more efficient dryers, they are finding it just makes sense to do it."
For more information contact:
Andrea Siy
SIY Communications
978-465-6363
andrea@siycommunications.com
Charlie Sears
Dri-Air Industries
860-627-5110
csears@dri-air.com