LG Logistics Revamp a Taste of What Australia Will Face
Share:
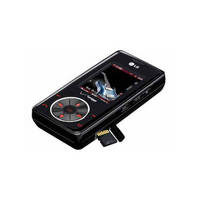
Logistics software specialist JDA (Australia) is pointing to key characteristics in the mature North America market for solid indication of what is around the corner for national retailers, food producers, and transport companies whose fleets cover the large land mass that is Australia.
Total logistics cost is a component of Australian business that can easily be better managed for increased profits, but JDA (Australia) urges we note the parallel experiences in a recent solution undertaken by LG Electronics and the management and movement of is manufactured consumer electronics, mobile communications products and home appliances in the USA.
The exercise identifies how a cleverly devised software platform not only delivers a level of logistics management that returns better profits, it provides complete quantification for this very pertinent element of the logistics supply chain.
The American arm of LG Electronics needed to establish integrated, best-practice workflows across its global transportation and distribution organisation. The company also needed to link variable market demand signals, distribution planning and transportation execution in order to reduce costs and increase resource and asset utilisation efficiencies.
An integrated business solution from JDA amalgamated the strengths of two of its software suites to achieve the optimised outcome for LG Electronics:
o JDA® Transportation & Logistics Management Solutions
o JDA® Agile Business Process Platform, now part of JDA® Enterprise Architecture
Gains for the client were immediate and highly transparent and quantified. The main business benefits were:
o Gain of a recurring 8% annual reduction in overall transportation and distribution costs
o Rapid time to value - solutions went live and delivered value in less than 32 weeks
o Significant service level and customer satisfaction enhancements
o Establishment of highly configurable supply chain management architecture to address future growth and regional management demands
LG Electronics' transportation division, with its annual expenses exceeding $40 million, was recognised as one of the critical areas within the company's operations that could deliver significant value to both the top and bottom line. LGE saw the ability to reduce transportation costs through synchronising planning and execution.
In order to extend the value of Oracle enterprise resource planning (ERP) and EXE warehouse management systems (WMS) deeper into the distribution network, LGE needed to integrate a best-of-breed transportation management system (TMS) into its existing enterprise management infrastructure.
This would enable LGE to achieve visibility into market demand variability and align it with its distribution and inventory planning operations. LGE's management team began by reengineering its business policies and processes to create more agile and adaptable supply chain operations.
The strategic objectives of this project concentrated on reducing transportation costs by raising the efficiency of LGE transportation resources and asset utilisation. Transportation costs account for approximately 51% of LGE's total logistics cost and was selected as the primary target area for reduction.
The first step was to redesign the company's transportation and delivery system. Linking variable market demand signals, distribution planning and transportation execution would enable LGE to optimally manage capacity and routings. The project scope became LGE's outbound logistics area including factory transportation, general delivery and home delivery.
Circumstances Driving Change
The LGE logistics network comprised three central distribution centres (CDCs), 18 regional distribution centres (RDCs) and more than 3,000 domestic consignees. In this environment, LGE builds more than 700 truck loads every day, 300 of which deliver to the CDCs with the remaining 400 delivered to the RDCs.
The two key issues facing management were the lack of quality and accessibility of accurate and timely information and the need to develop best-practice transportation and distribution management. LGE suffered from high levels of inaccurate shipment planning, inventory and capacity availability information, and as a result of this, disparate manual processes had been adopted.
Traditionally, critical service failures occurred due to significant demand variability and the communication lags between the various workstations across the organisation. Distribution and transportation processes were not synchronised and the resulting information bottlenecks translated into reactive management. LGE accounted for this inherent inefficiency through buffer inventories and disparate manual transportation planning. Both of these practices led to suboptimal results that had negative effects on both costs and service levels.
Load-building inefficiency, both in the time it took to create plans as well as plan quality itself, resulted in significant waste. Manual delivery plans were based upon fixed routing methodologies that did not factor in real-world variability and the associated cost ramifications of suboptimal asset assignment, causing inefficient capacity utilisation and driver assignment.
On the customer-facing end, drivers would make independent decisions affecting appointment time and routing as a trickle-down result of the siloed, manual decisions being made in the steps leading up to delivery. Without a dynamic methodology, static delivery runs concentrated orders in certain time and geographic zones instead of being based upon need or importance. All of these factors culminated into excess transportation costs and decreased service levels.
While LGE's management team recognised the need to streamline its business processes and identified multiple areas of improvement within its transportation and distribution operations, the challenge of achieving transparency and alignment between market demand variability and distribution planning and execution remained. Central to establishing integrated best-practice workflows across the entire transportation and distribution organisation was the need to implement an adaptable supply chain architecture that would effectively integrate the management of regional complexities with the deeper strategic value of LGE's enterprise planning and execution infrastructure.
Selecting JDA Transportation Management Solutions
After careful evaluation, LGE selected JDA's transportation planning and management solutions to specifically address order consolidation, dynamic hub selection and asset planning (continuous move) concerns. Although LGE's selection of these solutions was multifaceted, the primary deciding factor was the recognition of JDA's suite as the most complete and robust solution available on the market.
"JDA's advanced TMS is the only solution today that has the ability to deliver best-in-class supply chain management functionality along with the adaptability to customise workflows and scale across our complex and distributed supply chain network. This combination of world-class domain expertise, rich solution functionality and innovative delivery methodology works to extend the value of the JDA transportation management solutions both inside and outside of our enterprise and enables highly customisable and configurable user interfaces in an effective and cost-efficient manner," said Lee Geun An, chief officer, management innovation team, Hi-Logistics, LGE Logistics Subsidiary.
LGE was able to accelerate the implementation process through the use of sophisticated methodology in the JDA® Agile Business Process Platform (ABPP), a component of JDA® Enterprise Architecture. JDA ABPP improved the integrated development, testing and deployment environment and enabled the enhanced customisation of user interfaces, workflows and business logic while adding value to data staging and exceptions management.
In addition to the JDA solution's breadth and its implementation value, its flexibility was also far greater than other options evaluated. This flexibility was one of the essential factors in the decision-making process given the global reach of the LGE network and the substantial differences across geographies that would demand customisation.
Realising Significant Performance Gains
LGE was able to quickly deploy and configure the JDA solutions to meet its localised requirements, going live with the system in 32 weeks. Because of this, LGE realised immediate value and is able to self manage customised configuration of best practice workflows at all user levels.
The initial value target was a 4% reduction of transportation cost in RDCs and a 3% increase of load fill rate in CDCs through optimisation of transportation planning. Inventory turn has been accelerated through dynamic hub selection in transportation planning and increased collaboration between replenishment planners and distribution.
The company has also succeeded in synchronising intra-enterprise workflows across distributed operations, resulting in an 8% reduction in transportation and distribution expense. By interlinking the disconnected workflows across multiple internal organisations - including the workflows of transportation managers, inventory planners and customer- service representatives - LGE can now oversee distribution with a holistic view of both inventory and capacity as well as manage these resources against a single version of the truth.
Overall, LGE has realised tremendous efficiencies through its operational innovation powered by the JDA solutions, and continued improvements are expected in customer service levels as well as an ongoing annual cost savings of more than 8%.
"With JDA transportation management solutions, LGE was able to quickly accomplish integrated workflows between our existing systems infrastructure, including ERP, WMS, order management systems (OMS) and logistics management systems. The lead time for the deployment of JDA's TMS was 90% faster than if similar solutions were deployed through traditional development and integration methods," said Geun An.
For more information, please contact Ms Emma Hose.
JDA: Level 3/ 409 St Kilda Rd, Melbourne VIC 3000
Tel: 0401 149 735, email: Emma.Hose@jda.com
web: www.jda.com