Leading Systems Supplier for All Pipe and Thermoforming Sheet Extrusion Applications
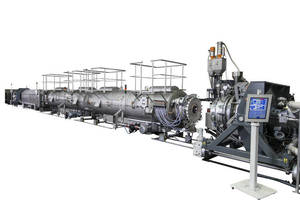
At its booth in Hall 13, A01, at Plast 2015, battenfeld-cincinnati will present a wide range of solutions for pipe extrusion – from PVC foam core pipe to PE-Xa pipes and the FDC system for automatic dimension change. In addition, the company's equipment for WPC/NFC extrusion, pelletizing and thermoforming sheet production will be showcased.
As an extrusion equipment specialist, battenfeld-cincinnati offers a portfolio of extruders with high performance, excellent homogenization and high energy efficiency.
For pipe extrusion, the twinEX series of parallel twin screw and the solEX series of single screw extruders are available, with output rates of up to 2,500 kg/h and 2,200 kg/h respectively. The best-selling plug play alpha single screw extruder is the perfect solution for standard applications, small pipes and technical profiles.
battenfeld-cincinnati also offers tailor-made, complete systems for WPC/NFC extrusion that are rounded off by wear-optimized metallurgical solutions. Recently, the cost-efficient fiberEX 93-34D extruder for medium outputs (up to 400 kg/h) was introduced. It is able to process a great variety of different formulations with just one plasticizing unit.
Powerful, flexible, quickly adjustable and cost-efficient pipe extrusion
With the company's newest equipment in FDC (fast dimension change) technology, it is possible to produce pipes of different diameters without stopping the line and thus save change-over standstill time and material costs. The FDC system is adjustable within a wide range of dimensions from 140 to 800 mm. The helix VSI-T+ pipe head with EAC internal pipe cooling ensures smooth pipe surfaces, optimal wall thickness distribution and roundness. Together with the active melt cooling system inside the die, the EAC system minimizes sagging. The other line components are also laid out for maximum flexibility and cost efficiency.
Multi-layer dies for flexible PVC foam core pipe production
Many pipe manufacturers replace their feedblock-pipe combinations with new multi-layer pipe dies for easier equipment handling in foam core pipe production. battenfeld-cincinnati recently introduced two spider 200-3 and spider 400-3 die models for this application. The dies are suitable for dimensions from 32 to 200 mm, or from 110 to 400 mm respectively, and permit throughputs from 350 to 1,200 kg/h. The spider pipe dies offer high performance, optimal layer thickness distribution with narrow tolerances and short dwell times thanks to short flow paths and a compact design. In addition, they are able to process a wide range of different materials and can also be converted easily for 2-layer applications.
Powerful, cost-efficient PE-Xa pipe extrusion lines
At an Open House in February 2015, battenfeld-cincinnati introduced a complete line tailored for PE-Xa processing. With an output of up to 150 kg/h, it can reach substantially higher throughput rates than conventional lines or RAM extruders with the added advantage of an extremely short, low-maintenance cross-linking station.
The counter-rotating parallel extruder model twinEX 93-28 PE-Xa and the RK32PEX pipe head were designed especially for this application. Via an elbow adapter, the pipes pass directly from the pipe head into a vertical infrared oven with eight IR heating elements for a high cross-linking rate at line speeds of up to 30 m/min.
Optimal extruder and roll stack combinations for ther-moforming sheet co-extrusion and barrier sheet extrusion
In battenfeld-cincinnati's multi-layer sheet extrusion lines, the main layers are plasticized by 75 mm high-speed single extruders, while 45 mm extruders produce the functional layers such as bonding adhesives and barrier materials, but also surface covers and high-gloss finish.
A feedblock-die combination ensures an even distribution of all layers, which is indispensable for a reliable barrier effect. The feedblock and die also feature an edge-encapsulating system for resource-saving processing of all materials.
A variety of roll stacks are available from battenfeld-cincinnati, of which the newest is the Multi-Touch roll stack. A unique roll configuration ensures consistent, uniform cooling on both sides of the sheet, even at maximum line speeds. This results in significantly improved sheet tolerances and stress-free sheet with optimal transparency, excellent flatness and a uniform thickness profile.
Flexible and efficient “EMS” technology for best pelletizing results
battenfeld-cincinnati also offers a range of counter-rotating twin screw extruders for flexible processing of PVC materials. The highlight of these machines is the "EMS" technology: it enables stepless adjustment of the back pressure gap and exact control of melt attributes at any time during production. This offers a wide processing window at optimal conditions, which results in excellent product quality. In addition, the barrel adjustment allows for processing of both soft and rigid PVC with one pair of screws with outputs of up to 1,800 kg/h. This saves energy and investment costs.
For further information visit us at Plast 2015, hall 13, booth A01.
Website: www.battenfeld-cincinnati.com
Youtube: www.youtube.com/BattenfeldCincinnati
About battenfeld-cincinnati:
The battenfeld-cincinnati group has five production locations on three continents and an extensive network of sales and service contacts. It ranks among the leading manufacturers of energy-efficient, high-performance extruders and complete extrusion lines for pipe, profile, sheet, thermoforming sheet and pelletizing according to customers' specifications.