Kremlin Rexson PU3000 Reduces Waste & Increases Production
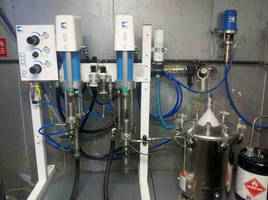
"The PU3000 has exceeded my expectations. I never thought it would work here. But now, I love it."
COMPANY: AUMA Actuators, Inc.
PRODUCTION: Working (2) shifts per day - these large and complex parts are continuously conveyed through the booth and coated by a single operator. The operator also mixed the material, and the material had a (1) hour pot life. This was constantly stopping production, affecting the loader & un-loader, the shipping department and ultimately, sales.
ECONOMIC INTEREST: At AUMA, the paint booth was the bottleneck. They needed to increase production, and reduce waste. They threw money away with paint waste. Consistency was also a concern. Mixing the material every hour across shifts created too many chances for errors. If the material wasn't mixed properly, it could not be packed as it came off the line. Not to mention, the issues to their reputation if the coating material failed in the field.
APPROACH: Sherwin Williams supplies the material and supports AUMA with equipment recommendations. Mark Miklos recognized the benefits a 2K machine could offer AUMA. Our Regional Manager, Tom Brown, and Mark justified a simple PU3000, with an estimated ROI of 8 months in labor and paint savings alone. This did not include the production increase. After a competitors demo failed, SW sent their demo unit along with their Tech Rep Randy French, and had the unit installed and painting within 30 minutes- with the first part, production ready.
CUSTOMER COMMENTS & KREMLIN REXSON SOLUTION:
No More Chemicals: "The best benefit is the significant reduction in exposure to the chemicals; I don't breathe in chemicals now. No paint on the arms, hands and body. Clothes are cleaner. The chemical exposure has been cut to almost nothing. That is the best benefit, " says the painter Dave Antonioli. He loves it! Every hour he needed to stop the line, and go into the mix kitchen to measure and mix paint, catalyst and solvents. Then use solvents to clean everything. "I would smell that all day long. Not anymore."
"I can be painting in 1 minute now": The first thing in the morning, Dave needed to mix paint and clean the measuring cups and sticks. Aside from smelling this first thing in the morning, it would take at least 10 minutes or longer to get the line moving. "Now we are ready to paint in less than 1 minute. Swipe the magnet and I am ready to go." He only goes into the mix room to check fluid levels. "Cleaning is just as easy. Swipe the magnet and 1 minute later the system is clean. Wipe the gun down, power down the machine and we are done." No more scrubbing pots and containers. He isn't the bottleneck anymore. All of that mixing time is now spent painting." Load at the start of the day and flush at the end.
Waste Reduction: "The PU3000 takes the guesswork out of the pot life. If I forgot the time I mixed the material, I had to guess on the pot life expiration. To avoid issues we would toss it and remix material, adding to waste." The PU3000 tracks the pot life time and notifies the operators as needed. This not only saves material but potential field issues from poor adhesion or damaged equipment. Most of all it cuts down the amount of material they throw out. They don't even flush for breaks or lunch now. Solvent use, paint use and hazardous waste costs have reduced significantly.
Previous Equipment:
Threw away about (8) quarts of waste paint, (16) liners, cups and sticks a day. Flushed for lunch, breaks, end of day and for pot life concerns.