Injection Molding Machines meet accuracy requirements.
Share:
Press Release Summary:
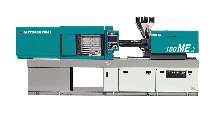
All-electric, Series MEt features RASMA-L frame, which suppresses vibration and holds accuracy to micron levels. Rigid clamping mechanism and double-roller supported, movable die plates promote precision. Super Resin Control-II ensures constant metering, while PLCS-10 control uses LAN for accurate communication between controller and servo motor amplifiers. Configurations range from 35-300 tons with max screw speed of 11.8 ips and max pressure of 34,128 psi.
Original Press Release:
MHI Injection Molding Machinery's MEt Series Meets Accuracy and Ease of Operation Requirements
Addison, IL - (April 10, 2003) MHI Injection Molding Machinery, Inc.'s new MEt Series of all-electric injection molding machines fulfills the injection molders demand for accuracy and ease of operation.
A variety of durable construction features enhance the accuracy of the MEt Series. MHI's newly developed RASMA-L frame (a lighter version of the company's original, proven RASMA), suppresses vibration, and holds accuracy to micron levels. The MEt's use of a highly rigid clamping mechanism and double-roller supported movable die plates further promote precision. To prevent tie-bar load imbalance during mold opening/closing operation, two nozzle-touch ball screws connect the MEt's injection and clamping units.
Design enhancements further contribute to Met precision. The incorporation of a Super Resin Control-II (SRC-II) works with other functions to ensure constant metering. Using the SRC-II system, the screw applies pressure to the melt after metering. This process results in high repeatability of melt density and product weight with every mold cycle. MHI offers an optional SRC-III system with shut ring control for even more exact metering.
For ease of operation, the MEt Series features a totally integrated PLCS-10 control panel. All settings and operations can be performed from this panel. The PLCS-10 uses Local Area Network to ensure accurate communication between the controller and each servo motor amplifier. The MEt's servo system is one of many efficiency-driven features. The MEt operates with 16% less energy consumption than competitor models and produces minimal noise.
The MEt is available in a range of configurations from 35 to 300 tons. Maximum screw speed is 11.8"/sec with a maximum pressure is 34,128psi.
To learn more about the MEt Series, visit MHI's booth #177 at NPE (June 23-27, 2003), or contact MHI Injection Molding Machinery, Inc., 1250 Greenbriar Drive, Suite B, Addison IL 60101, phone: (630) 693-4880, fax:(630) 693-0915, or visit their Web site at: www.mhiinj.com