Gas Analyzer enables advanced combustion control.
Share:
Press Release Summary:
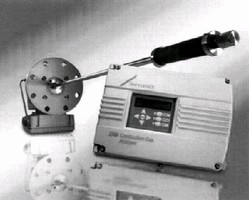
Designed for power generation and process industries, Model 2700C is fitted with zirconia based oxygen sensor capable of operating under harsh conditions and thick film combustibles sensor that measures changes in concentration of CO equivalents of less than 10 ppm. Sensors allow simultaneous analysis of O2 and CO without sample system. Both are located close to gas stream yet are virtually immune to corrosive and dusty samples as well as vibration found in power stations.
Original Press Release:
Servonex Announces The Launch of The New 2700C Combustion Gas Analyser, Designed For Advanced Combustion Control.
As part of Servomex's ongoing development programme, the company is launching the 2700C gas analyser, the latest in combustion gas analysers. It replaces the 2700B gas analyser, which established Servomex at the forefront of advanced combustion control. The new device has been developed specifically to meet the growing need for efficiency in the power generation and process industries.
The optimisation of the combustion process is critical to effective plant operation, as it allows significant reduction in fuel costs, while improving the environmental impact of the plant. However, providing the correct data for efficiency optimisation requires rapid response gas measurement For this reason, the Servomex 2700C analyser is fitted with a zirconia based oxygen sensor, capable of operating under the harsh conditions found in the power industry, and a patented 'thick film' combustibles sensor, which can measure changes in the concentration of CO equivalents of less than 10ppm. These tough yet sensitive sensors allow the fast and simultaneous analysis of O2 and CO without the need for a sample system. Both the sensors are located close to the gas stream yet are virtually immune to the corrosive and dusty sample as well as the excessive vibration found in power stations.
Servomex has worked with the US based Electric Power Research Institute (EPRI), one of the world's leading independent research institutes, to put the new analyser through extensive trials and ensure that it meets the demands of the market. These trials were used to verify the analyser's suitability for the analysis of O2 and CO in a flue gas in order to achieve efficient combustion control on a power plant.
During the six month trial period, the analyser operated totally reliably (the only one of three manufacturers units on test to do so), and the test indicated that zero calibration for the oxygen sensor and span calibration for both sensors was only required on an annual basis. Following an unexpected power-down during the tests, the analyser re-started and continued its analysis without significant change. The test results were used to predict a lifetime of seven years for the oxygen sensor, and five years for the combustibles sensor, when installed on a typical coal fired power station.
The rapid response time of the two sensors makes the 2700C gas analyser ideal for thermal power plants, especially as it is capable of measuring both oxygen and carbon monoxide at the same time. Commenting on the development of the new analyser, Tim Wilkes, Power Market Manager said, "The analyser was developed specifically for this market, and the results of the trials demonstrate just how suitable it is. The biggest challenges in these applications are typically dust, which causes blockages, high temperatures and corrosion, which shorten sensor life and dampen response, and cross sensitivity of combustibles sensors to non-combustible gases.
Our low flow, extractive architecture helped us to overcome the first two issues and our patented thick-film catalytic combustibles sensor shone through on the third area too. In fact though, the performance achieved in the EPRI tests and others at TUV in Germany, formed only an internal benchmark for our development team. Since then installation has been simplified and combustibles sensor performance improved even further over pellistor type designs. These enhancements are aimed at making customers cost of adoption lower and their payback period even smaller, via reduced fuel bills"
In addition to longer sensor life, the 2700C's architecture also allows it to work with a very wide selection of probes. Fitted as standard after a flame trap, probe materials include stainless steel, high temperature alloys and ceramics enabling operation from <700°C (1292F) to 1750°C (3182F) and filter, support, shroud and blow back options provide solutions from low to high dust loads.