Fluid Processor suits cleanroom applications.
Press Release Summary:
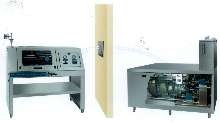
Stainless steel, split-system Microfluidizer® 600 and 700 model series can be set up so that operating assembly is in separate room from processing assembly; one hose, up to 30 ft long, runs through wall to connect separated assemblies. Processor reduces particles to sub-micron or droplet sizes, while intensifier pump drives product stream at velocities and pressures up to 40,000 psi through fixed-geometry microchannels.
Original Press Release:
Solve Clean Room Contamination And Noise Problems With New Split-System Microfluidics(TM) Microfluidizer® High Pressure Fluid Processors
Scaling up to production level, high-pressure fluid processors frequently cause atmospheric and noise level control problems for pharmaceutical, health care and chemical processors. The equipment's high-powered motors, built-in fans and high-pressure pumps affect the humidity, static, temperature, particulate, and decibel levels in hazardous material and class 100 or class 1,000 certified clean rooms.
To solve the contamination and noise problems, Microfluidics, a division of MFIC Corporation (Newton, MA), recently introduced a stainless steel, split-system Microfluidizer processor in its 600 and 700 model series. The new design allows operators to set up the processor's operating assembly (the motor, fan, hydraulics and oil) in a separate room from the processing assembly (intensifier pump and proprietary interaction chamber). A hose, up to 30 feet long, runs through the wall and connects the two assemblies. This split-system design is not available on alternative scale-up processors such as homogenizers that use belt and pulley operating systems.
By splitting the Microfluidizer processor's upper and lower assemblies, it is easier to control atmospheric conditions in the processing room. The processor fans no longer circulate contaminants in the clean room air, the risk of static sparks igniting hazardous material is lowered and decibel levels produced by the processing assembly are well below OSHA limits, so it eliminates the need for operator hearing protection.
Microfluidizer processors use a patented technology to reduce particles to sub-micron or droplet sizes at the highest shear rates available. Intensifier pumps drive the product stream at very high velocities and pressures up to 40,000 psi through patented, fixed-geometry microchannels. This process uniformly deagglomerates, disperses and distributes the particles to create very stable emulsions and suspensions. Optional equipment includes a removable cooling coil and cooling bath, a Steam-in-Place System for thorough sterilization of all processing surfaces, or a Clean-in-Place bypass system that quickly flushes the fixed-geometry interaction chamber between batches or before storage. Because there are no moving parts, no disassembly is required for cleaning.
Visit www.microfluidicscorp.com, E-mail mixinginfo@mfics.com, or contact Microfluidics at 800.370.5452 for a free laboratory batch test to determine how the new split-system Microfluidizer processor can improve your high-pressure fluid processing.