Customized Concepts for WPC
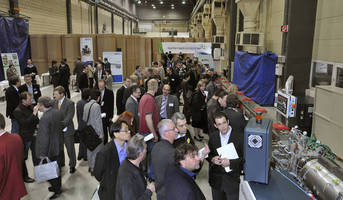
Leading machine supplier battenfeld-cincinnati again presents itself at Ligna
At this years' LIGNA fair in Hanover (hall 22, stand F 26), battenfeld-cincinnati Bad Oeynhausen/Vienna will be promoting the latest developments in its fiberEX machine series, especially designed for the processing of Wood Plastic Composites. Together with its partners Greiner Tool.Tec GmbH and Kompetenzzentrum Holz GmbH, battenfeld-cincinnati provides comprehensive solutions for complete extrusion lines as well as customized formulation development.
Since 2003, when Europe reached a sizeable market volume of 30,000 tons, the European market for Wood Plastic Composites (WPC) has continued to grow significantly. Annual growth rates of up to 25% are reported. In 2010, the European WPC market volume reached 140,000 tons. The product still dominating the market is Decking. The industry's next big challenge is to find new high volume applications for WPC. An example of a very promising approach is UK-based Tech-Wood International's housing concept which offers a do-it-yourself house building kit. The intention is to provide this kit for shelter homes and low cost housing for developing and emerging regions.
WPC can be processed either based on a one-step (direct extrusion) or a two-step process (compounding, followed by profile extrusion). Especially the European market faces a trend towards two-step production due to higher process stability and higher melt homogeneity, resulting in end products with optimized mechanical and physical properties.
When looking at the compounding part in the two-step process, three different methods are commonly available: using a heating-cooling mixer, a co-rotating twin screw extruder or a counter-rotating twin screw extruder. Each system is suited to different formulations and applications. Semi-finished products produced differ in particle size, particle size distribution and dust content, which also influences further processing behaviour. Above that, the energy consumption for the compounding step varies depending on the formulation processed. battenfeld-cincinnati recommends to its customers the technology best suited to the application at hand. For this, battenfeld-cincinnati relies on its many years of expertise and on the strong network of co-operation partners whose activities comprise the complete value chain for WPC.
State-of-the-art WPC profile extrusion targets line speeds of 1.5 - 2 m/min for conventional systems and up to 3.5 m/min for high performance extrusion solutions. Considering hollow decking as Europe's No. 1 application, these line speeds equal outputs of 250 - 300 kg/h up to 450 kg/h.
www.battenfeld-cincinnati.com
The leading extrusion equipment supplier shows its customized lines for WPC processing at its facility during the AMI WPC Conference in Vienna (this picture shows the 2010 event)