Custom Hot Runner Systems come fully mounted and wired.
Share:
Press Release Summary:
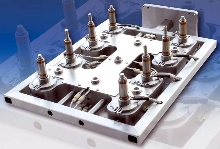
Featuring leak-proof connections between nozzles and manifold, H4015/... hot runner systems are available up to max 8 drops. Connecting cables of individual nozzles and hot runner are routed to terminal box via individually fabricated cable ducts, and fixed interlocking connection between nozzles and hot-runner manifold facilitates system assembly/disassembly. All nozzle lengths are exactly matched and mounted floating on hot runner to avoid deformation.
Original Press Release:
Fully Wired Hot Runner Systems H4015/...
Custom-made hot runner systems fully mounted and wired
The new H4015/... fully wired hot runner systems complement the extensive HASCO range of mounted standard systems, installation systems and hot sides with a further interesting component.
The main advantage of this new offer is the electrical wiring of the complete hot runner system carried out by qualified personnel. The connecting cables of the individual nozzles and the hot runner are routed to the terminal box via individually fabricated cable ducts where they are then wired according to the specifications of the customer. This avoids additional connection expense for the mould maker or injection moulder and guarantees a smooth start to production. The electrical safety and correct allocation of the zones to the manifold heaters and nozzles is ensured by HASCO and is documented in an individually compiled test report.
A further significant advantage is the fixed interlocking connection between nozzles and hot-runner manifold, which makes assembly and disassembly of the system considerably easier.
All nozzle lengths are exactly matched. In line with the established HASCO installation principle, the nozzles are not screwed to the manifold block, but are mounted floating on the hot runner. The inevitable deformation of the nozzles through radial heat expansion of the manifold, so critical with short nozzle lengths and large pitch centres, is avoided with this unique construction.
The nozzles can be positioned with "cold dimensions", which makes installation considerably easier. The heat expansion of the manifold beam occurring during heating is safely compensated by the floating bearing. Therefore, no bending torques or shear stresses occur in nozzle body. This increases the life cycle of the nozzles and the tool life of the sealing area. A secure seal for the system is guaranteed in the tool via the calculated thermal expansion of the nozzle head and manifold.
Assembly and disassembly of the system is made significantly easier through the structural design described above. This prevents damage to the hot runner during mould maintenance, and is also ensured by the mounting points on the manifold, which enable easy removal from the cavity plate. Distortion to the system due to tilting during removal are safely avoided.
The systems are individually designed, constructed and produced by HASCO in close coordination with the customer. HASCO can therefore guarantee dimensional accuracy and correct electrical wiring. We also guarantee it's leakproof between the nozzles and manifold.
When used in conjunction with the new Hasco nozzles Z33ff, it enables an easy and safely mountable hot runner system for the customer. The new Z33../... with screw-on caps further increases the mounting safety for such systems and minimises production hazards for the customer.
It also eliminates the processing expense for introducing the gate geometry and the front nozzle sealing area into the mould insert or mould plate, which represents a major simplification for long nozzles with small diameters. The sturdy and easy-to-produce fit diameter (tolerance H7) can easily be produced by conventional processing methods (jig boring).
The wired hot-runner systems H4015/... represent an optimum compromise between mounted systems and hot halves, in that they offer the advantages of the complete hot half H4400/... at an attractive price/performance ratio and extremely short delivery times.
Special features
- Complete electrical wiring and functional testing by HASCO
- Flexible design of the system according to customer specifications
- Simple installation in the nozzle-side of the mould
- Easy and safe disassembly and assembly during mould maintenance
- Guaranteed freedom from leaks between nozzles and manifold
- Guaranteed and tested electrical functioning and safety
- Available up to max. 8 drops
- Design of the system with tried-and-tested hot-runner nozzles Z33ff