Concurrent Engineering Helps Meet Thermal Challenges of High Speed Design
Share:
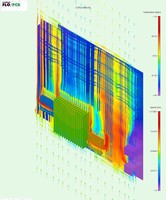
(November 17, 2006) -- With each successive generation of Cisco products, increases in functionality and speed have increased thermal design challenges. In response, Cisco Systems has defined a temperature aware design flow that significantly improves co-design between electrical and mechanical engineers. "The new concurrent electronic/thermal engineering approach has reduced the time required to identify and solve thermal problems, making it practical to address thermal issues at an earlier stage in the design process," said Herman Chu, Technical Leader for Cisco Systems, San Jose, California. "It appears that the five days that was required in the past to evaluate a prospective board design from a thermal standpoint can be reduced to only two and a half days or less."
The power consumption of the typical PCB has risen from 200 to 600 watts in just the past few years, raising thermal design from a relatively minor issue to a major design and reliability concern. The biggest problem with the old thermal design approach was the amount of time required to perform thermal modeling. It took about five days to generate first-pass results and most of this time was spent manually entering the data and often going back to the hardware architect and other electronics engineers to obtain missing information. Of course, while the initial thermal model was being created, the board design had often changed by enough to make the thermal model obsolete by the time it was created. Cisco thermal engineers believed that the key to improving this process was to automate the flow of information from hardware design to thermal engineering.
They learned of a tool with features that seemed to offer the opportunity to improve this process. This tool, called FLO/PCB, integrates with the PCB design software used by Cisco. It promotes a new design flow in which information is transferred seamlessly between the electronic and mechanical design processes. Designers begin by transferring information from the PCB design software to thermal analysis. A 3D computational fluid dynamics solver predicts airflow and temperature, for both sides of the board. Cooling management can thus be considered from the earliest stages of the design process. Placement updates made in thermal analysis can be passed back to PCB design thus providing bi-directional connectivity allowing for concurrent placement and thermal design.
The new concurrent electronic/thermal engineering approach has reduced the time required to identify and solve thermal problems, making it practical to address thermal issues at an earlier stage in the design process. The accuracy of the information used for thermal simulation has also been improved, increasing the accuracy of the simulation results. The savings are actually greater than this comparison reflects because shortening the time required to perform a thermal evaluation allows engineers to react faster and avoid putting additional time and money into a design with thermal problems. The greatest benefit of all is the additional revenues that can be generated by bringing the product to market sooner.
For more information, visit Flomerics' Web sites www.flopcb.com and www.flomerics.com.
Flomerics Inc.
US Headquarters
4 Mount Royal Ave., Suite 450
Marlborough, MA 01752
Tel: +1 (508) 357 2012
Fax: +1 (508) 357 2013
E-mail: info@flomerics.com
Web site: www.flomerics.com
FLOMERICS LIMITED
81 Bridge Road o Hampton Court
Surrey KT8 9HH o England
Tel: +44 (0) 20 8487 3000
E-Mail: info@flomerics.co.uk
Website: www.flomerics.com