Capacitive Motor Feedback Systems can replace resolvers.
Share:
Press Release Summary:
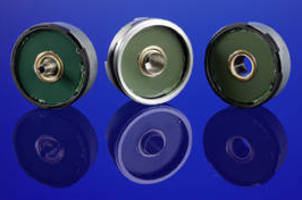
Supplied in 52 mm housing with HIPERFACE® interface, SEK/SEL52 series includes singleturn and multiturn versions with servo clamp, hollow shaft, or tapered shaft configurations. Bearing-less and capacitive sensor element delivers robust operations and accuracy of measurement is immune to radial and axial tolerances introduced during rotor rotation. Models provide 16 sine/cosine periods, resolution of 512 steps/revolution, and 1 (singleturn) or 4,096 (multiturn) steps/revolution.
Original Press Release:
New Capacitive Motor Feedback Systems are a Precise, Cost Effective and Space Saving Alternative to Resolvers
Bearing-less design delivers extreme robustness, while multiturn capability, electronic type label and HIPERFACE® Interface promise high performance
DAYTON, OH - SICK STEGMANN, INC. introduces SEK/SEL52 Capacitive Motor Feedback Systems. These high resolution motor feedback systems with HIPERFACE® interface come in a 52mm housing, and are available in singleturn and multiturn versions with servo clamp, hollow shaft or tapered shaft configurations. A unique bearing-less design delivers more robust operation than traditional motor feedback systems, while multiturn capability, electronic type label and HIPERFACE® interface promise significantly higher performance than traditional resolver options.
"At the heart of SEK/SEL52 motor feedback systems is a bearing-less, capacitive sensor element that is not only an attractively-priced alternative to the resolver, it also offers enormous technical benefits. Impulses are generated by a star-shaped rotor that changes, through its rotation, the dielectric material between the sender and receiver PCBs. The holistic scanning process means that neither radial nor axial tolerances introduced during rotor rotation can impair the accuracy of measurement. Moreover, the system configuration permits extremely low power consumption. In terms of robustness and precision, the SEK/SEL52 delivers the very features needed in the lower end segment of industrial position and speed determination applications," says, Jon Whittelsey, Application Engineer.
SEK/SEL52 motor feedback systems are ideal not only as an alternative in applications currently using resolvers, but where users need higher performance final positioning such as servo motors, handling drives, feed axis or standard robot applications. They are also well suited for use in traditional motor feedback applications that demand higher than normal robustness for reliable operation in high temperature and vibration environments common in textile machinery and mining applications, for example.
SEK/SEL52 motor feedback systems provide 16 sine/cosine periods, resolution of 512 steps per revolution, and 1 (singleturn) or 4096 (multiturn) steps per rev. They are rated for shock resistance to 100 g/10 ms, vibration resistance to 50 g/10 ... 2000 Hz, and provide reliable operation in temperatures ranging from -40...+115°C (singleturn) or -20 ...+115°C (multiturn).
The multiturn properties of the SEL versions are implemented using a mechanical gearbox in combination with magnets and Hall sensors, achieving absolute, non-volatile code and position determination. A crucial advantage over resolvers is that no external evaluation unit is required - all electronics are contained within an integrated ASIC.
Thanks to HIPERFACE, many popular servo drives have an interface standard that covers all applications needing only one type of signal line. Another advantage is the possibility of self-initialization and automatic controller parameterization of the drive system by using an electronic type label, as with the SRx motor feedback systems. Motor characteristics, serial and part numbers as well as further data which quickly help in case of service or exchange are written here. These can be used to independently adjust the controller to the parameters of the motor.
HIPERFACE is an eight wire interface standard that makes it possible to get commutation, speed regulation and position information from a single device. The physical interface includes two wires for an RS485 link, four wires for sine & cosine signals and two wires for the power supply; a reduction from as many as 19 leads in a traditional system.
HIPERFACE compatible motor feedback systems combine the functions of both incremental and absolute encoders. The absolute value in these systems is calculated only when the device is initially turned on, and is then transmitted via the RS-485 interface to a counter in the drive. The drive uses this initial absolute value for the commutation of the motor and also as a pointer to identify the exact period of the sine/cosine signals that the drive is currently evaluating. The drive then increases the base resolution of the sine/cosine signal by interpolating these signals in the drive with an A/D converter.
SICK STEGMANN, INC. is a wholly owned subsidiary of SICK AG in Waldkirch, Germany. SICK|STEGMANN is a world leader in the design and manufacture of incremental, absolute and linear encoders, as well as motor feedback systems.
SICK STEGMANN, INC., 7496 Webster Street, Dayton, OH 45414; (800) 811-9110; (937) 454-1956; fax: (937) 454-1955; sales@stegmann.com; www.stegmann.com.