Blow Molding Machine offers tie-barless accessibility.
Press Release Summary:
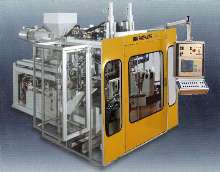
Shuttle Blow-Molding Machine, Model BW F4 can be configured for single or double stations, each allowing 1, 2, 3, or 4-parison molding of bottles ranging from 0.2-1.5 l capacity. Machine accepts molds up to 12.40 x 10.63 in., while providing 11.02 in. horizontal shuttle stroke and 5.91 in. max daylight opening. PC-based controller includes touch-screen interface, Windows graphic display, bus system, Ethernet connectivity, and tele-diagnostic capability.
Original Press Release:
New Uniloy BW F4 Shuttle Blow-Molding Machine Packs Max Productivity, Advanced Engineering into Small Footprint
Uniloy German engineering brings best practices to small machine design with tie-barless accessibility, in-machine trimming and labeling, closed loop precision, PC-based machine control, delivering higher output and changeover flexibility while using existing molds
July 2004 - Uniloy German engineering packs state-of-the-art technologies and maximum machine capability into the minimum possible footprint in the new Uniloy BW F4 shuttle blow-molding machine. Designed especially for the North American market, the new BW F4 meets needs for high flexibility, uptime and ROI by providing superior bottle processing efficiencies, fast changeover, and ease-of-use ergonomics - all at competitive pricing with dated technology machines. Smallest member of Uniloy's new F-type shuttle machine family, the BW F4 brings best practices to small machine design with tie-barless accessibility, in-machine trimming and labeling, and closed loop precision. The new Uniloy machine can be configured for single or double stations, each allowing one, two, three or four-parison molding of bottles ranging from 0.2 to 1.5 liter capacity.
A creative solution to upgrading operations and molding capabilities, the Uniloy BW F4 allows interchangeability with existing molds and configuration of touch-screen controls to resemble legacy machines. Size, precision and versatility make the BW F4 ideal for both prototyping and challenging production applications, while Uniloy backs the new machine with world-class application engineering and technical support.
The state-of-the-art BW design includes an advanced controller with color touch-screen operator interface, dynamic Windows graphic displays, bus system and Ethernet connectivity, and tele-diagnostic capability. Screens are available that closely resemble controls on legacy machines to avoid re-learning problems.
The BW F4 was carefully designed for mold interchangeability with legacy machines, allowing blowmolders to fully utilize existing molds and blowpins, even switch them back and forth with existing machines. "Done in one" capability speeds throughput and cuts total processing time by performing trimming and labeling within the machine, avoiding need for separate processes.
Maximizing capability in the minimum possible footprint, the single-station BW F4 measures just 106.3"W x 106.3" L x 157.5"H (2700 x 2700 x 4000 mm). The double-station model increases width to 126" (3200 mm) but stays the same in other dimensions, effectively doubling production while requiring just 27% more floor space. The Uniloy machines accept molds up to 12.40" long x 10.63" wide (315 mm x 270 mm) while providing 11.02" (280 mm) horizontal shuttle stroke and 5.91" (150 mm) max. daylight opening.
Designed for changeover ease and speed, the BW F4 supports trends to flexible, shorter-run blow-molding operations. Tiebar-less design speeds and simplifies mold changeover by allowing molds to be directly loaded into the machine. Doors on three sides permit installation from side or front. Door cut-outs enable die centering and blowpin adjustment while the machine is running for fast set-up and adjustment without interrupting production. Center-fed Willi Müller die heads allow quick color changes with reduced downtime and resin loss. The die heads deliver highly repeatable multi-parison performance with superior radial wall thickness control to minimize bottle weights and material usage.
In place of tie-bars, the BW F4 was engineered with a horizontal shuttle system running on precision guide rails. Offering superior precision over inclined shuttles, the rail system utilizes a rack-and-pinion synchronizer to ensure consistent platen parallelism under all load conditions. Closed-loop position and speed control of clamp and carriage eliminates hydraulic fluctuations and reduces component wear. Brushless DC extruder drives save 10% on energy consumption, while reducing wear and maintenance.
Full applications support is available through FGH Systems, Inc., Uniloy's North American shuttle solutions center. FGH Systems provides a comprehensive range of technical support services - bottle design, prototype molds, pilot production, blow mold tool engineering, manufacturing and qualification, process and systems engineering, equipment integration, machine installation and start-up. It is especially experienced at full turnkey project responsibility.
For more information on the Uniloy BW F4, contact: Rich Smith, Uniloy sales, tel: 734-428-2244or email: Richard_K_Smith@uniloy.com.