Batching Systems help minimize manual labor.
Press Release Summary:
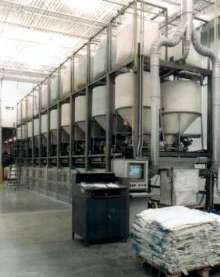
Original Press Release:
Automated Powder Batching System Reduces Manual Labor, Produces Exceptional Batch Consistency
Cincinnati, OH. September 14, 2004. Ingredient Masters, Inc. a manufacturer of custom material handling systems for ingredients used in the food/ beverage, pharmaceutical, chemical and ceramic industries, has introduced a family of batching systems for the efficient management of dry bulk, powdered, flaked and granular ingredients.
These automated powder batching systems are distinctive in several ways. First, the USDA polyethylene dispensers are round, with sides sloping to a shear wall drop. This design feature prevents the "bridging" effect, which is common in powder processing, and which complicates material flow.
The dispenser design has integral, centralized dust collection, but is designed to substantially reduce the generation of airborne dusts.
Systems incorporate the use of Super Sacks for incoming raw material. These polypropylene sacks hold up to 3000 lbs. of material, require less storage space and simplify issues of dunnage and landfilling. Super Sacks are mounted to a patented frame developed by Ingredient Masters and fork-lifted to the dispenser. This eliminates the injury risk and the time constraints of manual handling.
A rail-mounted scale cart, robotic device or AGV moves between dispensers; material is discharged into the cart through stainless steel pneumatic slide gates, according to the programmed recipe. Various vibratory devices can be used to assure optimum flow rate.
Load cells mounted on the vehicle are one of several ways the system assures exceptionally high batch accuracy. Ingredient Masters automated batching systems are PLC controlled; a graphic interface provides detailed overviews of system operation, ingredient usage and ingredient inventories, and tracks incoming lot numbers.
When a batch cycle is complete, the PLC produces a batch record that includes all ingredients and their respective weights, and assigns a batch lot number. Batch record data can be set to download automatically into a separate database. Material usage by day, week or month can be determined and protocols that allow operators to queue batches in a sequence, a week at a time, can be included.
Ingredient Masters automated batching systems use off-the-shelf hardware and software to prevent issues with proprietary equipment and platforms, and facilitate easy maintenance. Scales, conveyors and specialized product transfer equipment can be provided. Ingredient Masters turnkey systems are ISO compliant.
MORE INFORMATION FROM INGREDIENT MASTERS, INC. CINCINNATI, OH. (888) 345-4729 OR (513)231-7432 www.INGREDIENTMASTERS.COM