Monitoring and Controlling a Die Casting Press
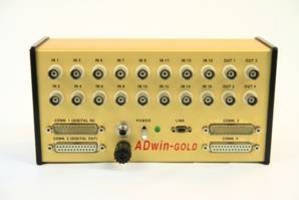
ADwin-Gold Provides Manufacturers With Real Time Data Acquisition
CHESTERLAND OH - CAS DataLoggers recently supplied the data acquisition and control solution for a prominent manufacturer operating die cast presses. These presses used hydraulic systems to force molten metal into a die, forming intricately-shaped parts requiring little final machining for use as engine components, transmissions and other parts.
Control over the injection process was often managed by a PLC--however, these conventional PLCs lacked adequate response times to maintain the tight control required during this process. It was critical to achieve fully formed parts of the proper density with minimum porosity while controlling the speed, volume and pressure during the injection process. Management saw the need for a stand-alone data acquisition system which could accurately monitor the pressure, force, speed and displacement in real-time during the shot injection and which also offered flexible communications capabilities for communication with a PC.
CAS DataLoggers custom-designed a solution for the customer that incorporated an ADwin-Gold Real-time Data Acquisition and Control System enclosed in a rugged metal housing. The ADwin system monitored and controlled the various parameters during the shot injection and was easily interfaced to a Visual Basic application providing the HMI for set-up and monitoring tasks including configuring the injection shot, viewing real-time data and storing data. All of the real-time control was achieved using the on-board analog and digital I/O of the ADwin system in real-time. This 16-channel system measuring at 12-bit resolution was then connected to various sensors to effectively monitor the pressure, force, speed and displacement during the injection shot.
The ADwin-Gold system's local real-time DSP CPU supported parallel, individually-controlled real-time processes while running independently of a PC's operating system, providing deterministic operation with 1 usecond or less response times. The ADwin's CPU also controlled signal acquisition and all measurements were recorded in real-time onto 16 MB of external DRAM for data storage. Flexible communication with a PC was enabled via the system's integrated Ethernet and USB interface.
The ADwin software environment was able to operate using Windows, LINUX, or as a stand-alone data acquisition system. Multiple PCs communicated with the ADwin-Gold concurrently during program implementation and commissioning, and when necessary, one PC could also access multiple ADwin systems, as part of a network to provide centralized monitoring. The system also enabled calibration of the system's analog inputs and outputs and had drivers for many popular programming environments including VB, VC/C++, LabVIEW, TestPoint and others.
Real-time development was provided by ADbasic and ADtools: with ADbasic, users defined the processing sequences executed on the ADwin hardware, optimizing and compiling the program code with just a click of the mouse. The system's real-time processes executed independently after being loaded on the ADwin-Gold via ADbasic or a graphical PC user interface. ADbasic also contained the functions to access all inputs and outputs as well as those for floating-point operations, process control and PC communication.
Users also had a library containing standard functions such as for filtering, various examples for counter use, function generators etc., which helped them to quickly implement the program. ADtools offered an easily configurable way for users to view their real-time data graphically or numerically to visualize process sequencings or to set input values via potentiometers, sliders, or push buttons. Additionally, ADtools constantly provided the current status of the ADwin system's resources.
The manufacturer's shot injection process was effectively monitored and controlled following installation of the ADwin-Gold data acquisition system. The ADwin provided highly accurate, real-time control of the shot injection and was easily customized to provide special functionality, resulting in faster performance than was possible using conventional PLCs. Operators used a Windows-based PC for the HMI to greatly simplify connection to the factory network for monitoring, recipe management and process feedback-this oversight gave users the split-second response times needed to ensure the correct part density and porosity. Additionally, data transmission and accessibility were greatly simplified via the system's flexible communications capabilities.
For more information on the ADwin-Gold Real-time Data Acquisition System, other sophisticated data acquisition and control solutions from ADwin, or to find the ideal solution for your application-specific needs, contact a CAS Data Logger Applications Specialist at (800) 956-4437 or visit the website at www.dataloggerinc.com.
Contact Information:
CAS DataLoggers, Inc.
12628 Chillicothe Road
Chesterland, Ohio 44026
(440) 729-2570
(800) 956-4437
sales@dataloggerinc.com
http://www.dataloggerinc.com