Thermoplastic Composites combine long glass and carbon fiber.
Press Release Summary:
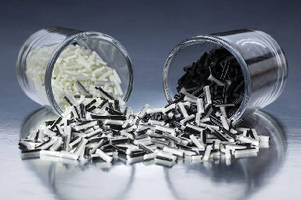
Suitable for consumer and sporting goods, Hybrid Thermoplastic Composites combine long glass fiber and long carbon fiber reinforcement together in single, ready-to-mold composite pellet. Nylon 6/6 hybrid 40% long glass+carbon fiber reinforced composite with 20% carbon fiber and 20% glass fiber has tensile strength of 41,200 psi and flexural modulus of 2,600 ksi. Inclusion of long glass fiber allows material to retain 78% of un-notched impact capability of glass at 18.8 ft-lb/in.
Original Press Release:
PlastiComp Fills Long Fiber Performance Gap with Development of Hybrid Long Glass+Carbon Fiber Thermoplastic Composites
WINONA, MINN., USA — PlastiComp, Inc., a global leader in long fiber thermoplastic (LFT) materials and technologies, has developed an innovative set of hybrid thermoplastic composites that combine long glass fiber and long carbon fiber reinforcement together in a single, ready-to-mold composite pellet. The new products expand the performance range of long fiber material options available to product designers while offering a cost effective avenue to adopt the high performance capabilities of carbon fiber.
“PlastiComp’s new hybrid long glass+carbon fiber reinforced products really hit a sweet spot that nicely bridge the performance gap between using either of these fibers by themselves,” said Eric Wollan, business development manager at PlastiComp. “The carbon fiber significantly boosts strength and stiffness while the glass fiber allows the toughness that many choose LFT materials for to be retained. Strength and toughness are key long fiber attributes that can’t be achieved in unison with other reinforcement methods.”
A nylon 6/6 hybrid 40% long glass+carbon fiber reinforced composite with 20% carbon fiber and 20% glass fiber has a tensile strength of 41,200 psi (284 MPa), which is 96% that of an equivalently loaded long carbon fiber material and 24% higher than a similar long glass fiber material. It possesses a flexural modulus of 2,600 ksi (17,931 MPa), which is 87% that of carbon and 86% higher than glass. The inclusion of long glass fiber allows the material to retain 78% of the un-notched impact capability of glass at 18.8 ft•lb/in (1,004 J/m), which is a 25% improvement over carbon alone.
 | 40% Long Glass Fiber PA6/6 | Hybrid 40% Long Glass+Carbon Fiber PA6/6 | 40% Long Carbon Fiber PA6/6 |
Specific Gravity | 1.45 | 1.40 | 1.31 |
Tensile Strength | 33,300 psi 230 MPa | 41,200 psi 284 MPa | 43,000 psi 297 MPa |
Tensile Modulus | 1,700 ksi 11,724 MPa | 3,500 ksi 24,138 MPa | 4,500 ksi 31,034 MPa |
Flexural Strength | 47,500 psi 328 MPa | 58,700 psi 405 MPa | 66,000 psi 455 MPa |
Flexural Modulus | 1,400 ksi 9,655 MPa | 2,600 ksi 17,931 MPa | 3,000 ksi 20,690 MPa |
Un-notched Impact | 24.0 ft•lb/in 1,282 J/m | 18.8 ft•lb/in 1,004 J/m | 15.0 ft•lb/in 801 J/m |
Deflection Temperature @ 264 psi (1,820 kPa) | 490 °F 254 °C | 490 °F 254 °C | 485 °F 252 °C  |
  Â
“There is an interesting synergy taking place in these hybrid long glass+carbon fiber composites,” said Wollan, “we can cut the amount of carbon fiber used in half and still keep 85-95% of the strength and stiffness, plus the addition of glass fiber is bumping up the durability by up to 25%. That performance combination really makes these products attractive, because they land right where a lot of people need to be to use LFT composites as substitutes for metals.”
“Although long carbon fiber reinforced composites are the pinnacle of thermoplastic performance, economically their use can’t be justified in a lot of applications,” said Wollan. “Now, with these new hybrid long glass+carbon fiber composites, PlastiComp has a stepping stone material in the middle of the glass fiber to carbon fiber gap that can be 20-50% less expensive with hardly any performance hit.”
PlastiComp can customize the percentage combinations of glass and carbon fiber in these hybrid LFT materials to tailor performance and cost to meet individual application specifications across any market segment. They are especially advantageous to consumer and sporting goods products where the inclusion of carbon fiber allows them to be marketed as utilizing high performance composites and obtain a price premium. The cost/benefit ratio of these composites should be attractive to the automotive and transportation industries that are aggressively trying to reduce weight for improved fuel economy and lower emissions. They are strong contenders for under-the-hood components that require elevated temperature and load bearing capabilities.
PlastiComp manufactures its LFT Complçt® composite pellets using an optimized pultrusion process that maximizes resin and fiber bonding to obtain the highest possible mechanical properties. Hybrid long glass+carbon and other LFT composites from PlastiComp are made-to-order in polymers from polypropylene to PEEK.Â
As a vertical, full-service long fiber compounder, PlastiComp can provide design and analysis services when converting applications to new materials as well as partnering with OEMs on new product development programs to customize LFT materials and processes to meet specific performance criteria.
For more information on PlastiComp’s LFT products and technologies, please call +1 507-858-0330, e-mail info@plasticomp.com, or visit their website at www.plasticomp.com.
Complçt® is a registered trademark of PlastiComp, Inc.
About PlastiComp
PlastiComp, Inc. focuses on developing and providing long fiber reinforced thermoplastic composite technologies to partners worldwide. These include ready-to-process reinforced LFT (long fiber thermoplastic) pelletized compounds, along with process development and manufacturing equipment licensing for LFT pultrusion, in-line D-LFT (direct long fiber thermoplastic) Pushtrusion™, and in-line D-GMT™ (direct glass mat thermoplastic) technologies. PlastiComp’s injection moldable Complçt® LFT composite compounds are available as standard and custom formulations in resins from polypropylene to PEEK.