Multi-Roller Polishing Stack enhances production of film.
Press Release Summary:
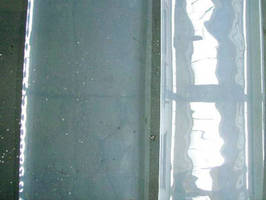
Multi-Touch polishing stack helps film producers optimize transparency, flatness, and thickness uniformity for materials such as PS, PET, and PP as well as EVA or laminated products. Two-roll polishing stack, used for preliminary calibration, is followed by 3, 5, or 7 rolls for final calibration. Design provides even, consistent contact between film and rolls, even at maximum line speeds, which ensures optimal cooling of both sides of film.
Original Press Release:
Optimal Contact Between Rollers and Film Fields Improved Transparency
Multi-Touch polishing stack combines many advantages for high-performance processes
With its new Multi-Touch polishing stack, battenfeld-cincinnati, Bad Oeynhausen/Vienna has developed an optimal solution for film producers who are not prepared to compromise on film quality even at high line speeds. Thanks to an absolutely innovative con-cept, a high degree of transparency, excellent flatness and an ex-tremely even film thickness can now be achieved for a great varie-ty of materials, such as PS, PET or PP, as well as EVA or laminated products.
As is the case in all sectors of the extrusion industry, outstanding efficiency in the production process is also a must in film extrusion today. The demand is for higher and higher output with optimized product quality. Criteria such as transparency, high gloss and flat-ness are vital factors especially in the production of packaging sheet for thermoformed products. At the same time, film and sheet producers want to be able to respond as flexibly as possible to the diversity of incoming orders.
As a supplier of complete film and sheet extrusion equipment with many year of experience, battenfeld-cincinnati can draw on an enormous wealth of expertise, which it utilizes to optimize various machine components and to adapt them to latest requirements. With its Multi-Touch polishing stack, the machine manufacturer is breaking completely new ground, extending its product portfolio by adding a solution for high-end applications in terms of both quantity and quality.
The main idea in the design of this new polishing stack was derived from the theoretical assumption that infinite line speeds could be realized with an infinite number of gaps for final calibration. In the Multi-Touch polishing stack, this idea has been put into practice with a two-roll polishing stack for preliminary calibration, followed by three, five or seven rolls for final calibration. The first two rolls come with a large diameter to minimize deflection. They are followed by smaller rolls in order to achieve flat, stress-free film and sheet. In contrast to the well-established, conventional three-roll polishing stacks, the Multi-Touch polishing stack thus provides absolutely even, consistent contact between the film and the rolls even at maximum line speeds, which ensures optimal cooling of both sides of the film. The greater number of post-cooling gaps provide a reliable means to even out film thickness tolerances. In this way, film can be produced with maximum transparency, excellent flatness with only few orientations, and a uniform thickness profile.
Thin-walled chill rolls with small roll diameters are used to facilitate easy handling, with a simultaneous increase in cooling per-formance. They offer the same hardness and line load capacity as conventional rolls, yet operate significantly more efficiently.
battenfeld-cincinnati already built the first prototypes of this inno-vative polishing stack in 2008. It was subsequently tested in pro-duction and then still further optimized. The first Multi-Touch po-lishing stack has been up and running on the production floor of a major German film producer since autumn 2011. The customer is enthusiastic about it. The polishing stack is now available with up to 7 post-cooling chill rolls for outputs of up to 3,600 kg/h for PP.
www.battenfeld-cincinnati.com