Ultrasonic Punching/Sealing Machine saves production steps.
Press Release Summary:
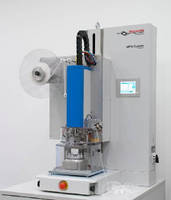
In one step, HiQ MPW transports membrane belt by conveyor, punches membrane contour, and welds membrane onto part, saving material and cutting cycle time to less than 2 seconds per weld cycle. Modular Weld Punch machine is equipped with vacuum monitor that checks whether membrane is correctly punched and positioned. Machine control also features gentle conveyor transport with splice check, which minimizes other sources of error and potential production downtime.
Original Press Release:
The New Herrmann HiQ MPW Ultrasonic Punching/Sealing Machine Saves Material and Steps in the Production Process
Simultaneous ultrasonic punching and welding for membranes
The number of plastic components with integrated membranes is on the rise. These membranes are either used in the automotive industry as pressure-compensating elements which protect against condensate and compensate for changes in pressure, or they are used as filter media in technical medical components and consumer items.
Until now two steps were needed to process the membranes. Firstly the previously assembled membranes had to be removed from a carrier belt by means of vacuum handling and supplied to the ultrasonic welding tool (sonotrode) to then be welded onto the plastic component via the pneumatic sealing stroke.
The HiQ MPW (Modular Punch Weld) machine, a new technical development from ultrasonic specialist Herrmann Ultrasonics, can punch and weld at the same time. A cheaper membrane material belt of 5 – 22 mm can therefore be used as the membrane does not have to be tailored in advance.
In one single step, the unit:
1. transports the membrane belt by conveyor
2. punches the membrane contour
3. welds the membrane onto the part
This saves material and reduces the cycle time to less than 2 seconds per weld cycle which translates into a major improvement in OEE (Overall Equipment Efficiency).
The standard optical quality control previously undertaken downstream is not needed because the MPW system has a vacuum monitor to reliably check whether the membrane is correctly punched and positioned. The machine control also features gentle conveyor transport with a splice check which reduces other sources of error and therefore potential production downtime. A special position measuring system for high cycle rates is wear-free. The Herrmann MPW unit can be flexibly integrated into automation lines or supplied as a manual work station.
The fully integrated work station will be shown at the MD&M WEST (booth # 3235) in Anaheim, CA.
Herrmann Ultrasonics, Inc. partnered with the company Oxyphen in Switzerland. Oxyphen is the leading manufacturer of microporous track-etched membranes and membrane products. For more than two decades Oxyphen has developed and manufactured customized membranes and membrane devices for applications in automotive, life science, as well as for industrial applications. Mr. Peter Terstappen with Oxyphen (Head of Product Management) will be at our MD&M WEST booth
# 3235.
Benefits of ultrasound in membrane welding
When membranes are ultrasonically welded, plastic melt flows out of the plastic material into the membrane's textile matrix. The specific energy input and defined melt formation ensure that the membrane is not damaged and that the weld withstands the application requirements. After the ultrasonic process, the membrane can be loaded right away and the component processed further. Additional substances such as adhesive or mechanical mounting brackets are not needed. Given the short cycle times, ultrasonic welding is ideal for mass production.