Sterilization System extends life of machine tool coolant.
Share:
Press Release Summary:
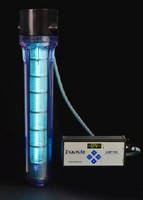
Combining UV light with customizable filter, ASF 100 Industrial Aqueous Sterilization System controls spread of bacteria, mold, and fungi while removing unwanted particles from aqueous industrial fluids. Chemical-free system can be integrated into most machine tools that use aqueous liquids at temperatures up to 125°F with tank volumes up to 120 gal. Built-in electronics designed for industrial environments offer variety of operation modes and provide visual alerts when maintenance is required.
Original Press Release:
Inauvate Introduces the ASF 100 Industrial Aqueous Sterilization System
Marlborough, Massachusetts, -- Inauvate Work Solutions introduces a novel, chemical-free UV light bacteria sterilization system designed to extend the life of machine tool coolant.
Monday morning stink caused by excessive bacteria in machine tool coolant is a common problem in manufacturing. Inauvate has developed the chemical-free ASF 100 which combines an ultraviolet (UV) light with a customizable filter to control the spread of bacteria, mold and fungi while removing unwanted particles from aqueous industrial fluids. This prolongs fluid life leading to fewer change outs per year, lower disposal cost, and reduced machine downtime.
Inauvate’s ASF 100 is compact, easy to install, and made specifically for the manufacturing industry. It can be easily integrated into most machine tools that use aqueous liquids at temperatures of up to 125°F (51°C) with tank volumes of up to 120 gallons. For applications with sump sizes over 120 gallons, multiple units can be installed in tandem to provide adequate disinfection. The ASF 100 can work in conjunction with portable oil removal equipment, such as skimmers and coalescers, for increased fluid cleanliness.
“Green” benefits of the ASF 100 include reduced waste, minimal energy costs, and a cleaner and healthier work environment. As a chemical-free system, it eliminates the need to use traditional harsh chemicals that can negatively affect performance of the work fluid, reducing cost and environmental waste. This is especially useful in heavily-regulated industries and locales, where common industrial chemical additives may be prohibited. A built-in safety interlock protects personnel from inadvertent exposure to UV radiation.
The ASF 100 relies on a multi-pass recirculating configuration and a directed flow through the filter unit to maximize UV exposure. Normal output models are ideally suited for use on aqueous parts washers and other systems utilizing transparent fluids. Opaque fluids, such as many metal-cutting coolants, do not transmit UVC waves as easily and thus require the use of a high-output UV disinfection model to be most effective. High-output models also include a bulb-monitoring feature to ensure that the UV bulb is lit which is ideal for applications where the opacity of the fluid prevents it from being checked visually. Sumps are available in a 10” size for compact installations and a 20” size for maximum light exposure and effectiveness.
The filter element helps to remove small chips from the coolant stream that can cause premature tool wear and degrade surface finish. It also protects the light surface from exposure to contaminants that can scratch its surface degrading performance of the UV system. Filters are made of stainless steel construction, allowing them to withstand harsh environments and multiple cleanings, and are available in standard 375, 540 and 840 micron sizes with custom sizes available by special order.
Built-in electronics designed specifically for industrial environments allow for a variety of operation modes and visual alerts to the user when maintenance is required. A fully-programmable built-in timer allows the ASF 100 to be customized to fit any shop schedule and can act as a stand-alone unit with the capability to control an auxiliary pump. The ASF 100 can also be externally controlled, for example by a CNC machine using M code relays, with an optional I/O cable. Sensors monitor the environment inside the filter unit and will adjust the output of the UV bulb to minimize particulate build-up and the resulting maintenance required to maintain the system’s effectiveness. Visual notifications alert the user when common maintenance tasks such as filter cleaning, bulb cleaning, and bulb replacements must be performed.
Inauvate Work Solutions offers tools for manufacturers that reduce costs, increase productivity, and contribute to a better environment. A brainchild of Ruland Manufacturing Co., Inc., Inauvate was founded to share products developed to improve operations on the Ruland factory floor. “We have found that a common sense approach to workplace organization and reduced waste contributes as much to profitability, product quality, and the environment as do more costly investments,” explains William Hewitson, Vice President of Operations at Ruland in Marlborough, Massachusetts. “This has helped Ruland to thrive while continuing to manufacture all of its products in a ‘high cost’ location with strict environmental standards. Our newest development, Inauvate’s ASF 100, pays for itself in months, not years.”
Inauvate at IMTS 2014, International Manufacturing Technology Show, 8 to 13 September 2014, McCormick Place, Chicago: Booth W-1952, Pavilion Tooling & Workholding Systems
About Inauvate Work Solutions:
Inauvate Work Solutions offers tools for manufacturers that reduce costs and increase productivity, and contribute to a better environment. A brainchild of Ruland Manufacturing Co., Inc., Inauvate was founded to share products developed to improve operations on the Ruland factory floor. Ruland Manufacturing Co., Inc. was established in 1937 as a manufacturer of precision components. Ruland’s focus for the past 40 years has been on high performing shaft collars and couplings. All Ruland products are carefully manufactured in Ruland’s factory in Marlborough, Massachusetts, USA, under strict controls using proprietary processes. The complete product line includes shaft collars and rigid couplings, and a full assortment of motion control couplings: beam couplings, bellows couplings, oldham couplings, miniature disc couplings and zero backlash jaw couplings.