Machining Center uses 30-taper spindle tooling.
Share:
Press Release Summary:
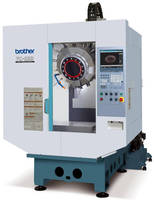
Optimized for rigidity and accuracy, TC-S2D machining center comes in 3 models with 300 kg max table load and 300, 500 or 700 mm X-axis; 360-400 mm Y-axis; and 300 mm Z-axis travels. Servo-driven tool turret, together with spindle acceleration/deceleration rates, allows one tool rotating at 10,000 rpm to be replaced in 1.6 sec with adjacent tool accelerated to same speed. Furthest tool in turret, necessitating 180° indexing, is exchanged in 2.4 sec.
Original Press Release:
Think 30-Taper for High Productivity and Low Emissions, Says Brother
Compared with 40-taper machining centres, Brother's new 30-taper model is 40 per cent more productive and four times less polluting
The Japanese machine tool manufacturer, Brother, which specialises in building machining centres that use 30-taper spindle tooling, has unveiled a new model that takes speed of operation and power consumption to unrivalled levels of efficiency. Celebrating its 100th anniversary in 2008, Brother sold its 50,000th machine in July despite having started production as recently as 1985.
Sole UK agent, Whitehouse Machine Tools, which was present at the launch of the new TC-S2D machining centre during JIMTOF 2008 (Tokyo, 30th Oct - 4th Nov), reports on the attributes of the faster and greener Brother model. Traditionally, such machines were called tapping or drill/tap centres, but raised specification over recent years has endowed them with sufficient milling power and rigidity for them to be regarded as machining centres.
A key benefit for the TC-S2D user is the servo-driven tool turret, which together with rapid acc/dec of the spindle allows one tool rotating at 10,000 rpm to be replaced in 1.6 seconds with the adjacent tool accelerated to the same speed, compared with typically 2.9 seconds on competitors' machines. Even the furthest tool in the turret, necessitating 180 degree indexing, is exchanged in 2.4 seconds, around one-third faster than average. Chip-to-chip times are also fast, as tool change takes place without stopping the Z-axis feed.
Tim Whitehouse, a member of the second generation management team at Whitehouse Machine Tools, points out that even on quick machining centres, automatic tool change accounts for approximately 20 per cent of overall cycle times. The TC-S2D is consequently capable of substantially raised levels of productivity.
In one test, albeit machining a component that played to the strengths of the TC-S2D, production output was 40 per cent higher than on the fastest 40-taper machining centre on the market. The cycle used nine tools and involved drilling 12 holes of 5.1 mm diameter, M6 rigid tapping of all holes, spot facing in seven locations and boring in two locations.
Other factors leading to short idle times are 50 m/min rapids in all linear axes, cutting feeds of 10 m/min in X / Y and 20 m/min in Z, and a 16,000 rpm spindle option.
As far as the environment is concerned, the TC-S2D is one of the least polluting machine tools in the world. It uses 60 per cent less electricity to produce the compressed air consumed, compared with the pre-existing Brother TC-S2C; and 70 per cent less than the best of the 30-taper competition. Power consumed by other machine functions is down by 40 per cent.
These figures translate into 15 per cent lower CO2 emission than the TC-S2C and 45 per cent less than the greenest 30-taper machine from other manufacturers.
Compared with equivalent 40-taper machines, the reduction in this greenhouse gas is fourfold. Based on annual production of 50,000 components, Brother calculates that whereas the amount of CO2 emitted by a 40-taper machine would be 6.8 tonnes, a TC-S2D produces just 1.7 tonnes, a saving equivalent to the absorptive capacity of 720 mature cedar trees.
Various other improvements have been made to the latest model, including a redesign of the machine structure using finite element analysis to improve rigidity and accuracy. Roundness of 1.1 microns can be achieved when boring a hole in aluminium, for example. There has been a significant reduction in the number of parts used in the construction of the new machine, leading to increased reliability. Swarf removal from the working area has also been improved.
Extra safety features have been introduced in terms of additional limit switches and interlocks, while at the control, access to functions is hierarchical according to the seniority of the operator. The CNC-B00 can control five axes, including the two rotational axes of a compound table. Both conversational and G-code programming are possible.
There are three TC-S2D models in the range with X-axis travels of 300, 500 or 700 mm. The smallest machine, a new version with 14 positions in the turret but no 21-tool option, was not available in the -S2C series. The Y-axis on all models is up from 360 to 400 mm compared with the TC-S2C, while the vertical Z-axis movement of the turret remains the same at 300 mm. Maximum table load has been increased from 250 to 300 kg.
On behalf of: Whitehouse Machine Tools Ltd,
Princes Drive, Crackley Industrial Estate,
Kenilworth, Warwickshire, CV8 2FD.
Tel: 01926 852725. Fax: 01926 850620.
E-mail: timw@wmtcnc.com
Web: www.wmtcnc.com
Contact: Tim Whitehouse.
Issued by: THE RIGHT IMAGE Ltd,
PO Box 42, Twickenham, TW1 1BQ.
Tel: 020 8891 0603.
E-mail: therightimage@aol.com
Contact: Chris Wright.