Evaporation Boats provide corrosion resistance.
Share:
Press Release Summary:
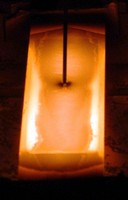
Able to withstand temperatures of 1,500°C or more, VaporStar Intermetallic Composite Evaporation Boats resist corrosion from different metals and provide even wet-out for consistency of deposition on substrate. They stay wettable throughout their life, even after grooving and slag build up that is typical after long periods of metallization. Thermal shock resistance enables boats to resist cracking during initial heating.
Original Press Release:
GE's VaporStar* IMC Evaporation Boats Combine Excellent Wettability and Corrosion Resistance with Extended Life
MYRTLE BEACH, S.C. - Oct. 16, 2005 - The vacuum metallization process, used to deposit a thin layer of metal on a wide array of substrates from polyethylene terephthalate (PET) plastic film to TV picture tubes, relies on evaporation boats that heat aluminum and other metals to the vaporization point. In this extremely demanding production environment, evaporation boats must withstand temperatures of 1500 C or more, resist corrosion from different metals, and provide even wet-out for consistency of deposition on the substrate. GE's Advanced Materials' Quartz business has developed a new grade, in its Metallist* line of intermetallic composite (IMC) evaporation boats, that is intended to meet all these challenges while providing up to 65 percent longer life than competitive boats. The superior properties of GE's VaporStar* IMC evaporation boats can give manufacturers critical advantages including higher-quality end products, higher productivity, faster cycle times, and greater value.
"VaporStar IMC boats represent a true breakthrough in material science," said Greg Strosaker, GE product manager, Ceramic Powders and Shapes. "First, by providing both high corrosion resistance and high wettability, our new VaporStar grade resolves the traditional dilemma of choosing between these two properties. Second, longer boat life means fewer changeovers and more production time. Finally, the boats' ease-of-use and higher operating stability deliver the potential for improving metallizing quality and yields. We believe these performance advantages will help customers become more competitive."
Using its Design for Six Sigma process, GE worked with a number of key customers throughout its development of the VaporStar boats, and conducted extensive validation with customers to substantiate that the benefits delivered by the boats were significant and present in real-world operating conditions, not just in a controlled laboratory environment. The company built a laboratory chamber to replicate customers' process environments and developed special tests to quantify wetting and corrosion characteristics. Quantitative field testing was conducted at more than 10 customer sites.
Results of these tests indicate VaporStar IMC boats provide up to twice the wettability of existing two-part boats with the same high corrosion resistance. Higher wettability leads to more consistent aluminum deposition and higher-quality metallized products. Further, VaporStar boats stay wettable throughout their life, even after the grooving and slag build up that is typical after long periods of metallization. These improvements can translate to longer life. When benchmarked against current products, the GE boats achieved up to 65 percent longer life vs. two- and three-part boats. Improved thermal shock resistance compared to other two-part products provides greater resistance to cracking during initial heating.
For operators, the increased wettability of VaporStar IMC boats means improved ease of use and better control over the metallizing process. Operators who participated in GE testing consistently reported greater plate uniformity and aluminum puddle stability over the complete life cycle of the VaporStar boats.
GE is committed to helping customers discover the benefits of VaporStar boat technology in their processes, offering training on the use of VaporStar boats, benchmarking studies to define baseline performance of existing boats, and tests to demonstrate the improvements possible through VaporStar boats.
The VaporStar grade joins two existing Metallist products: Classic* IMC grade and StabilizerPlus* IMC grade. The new product is available immediately from GE, in typical resistivity ranges required for vacuum metallizing processes.
About GE Advanced Materials
The Advanced Materials business of General Electric Company is headquartered in Wilton, Conn. Advanced Materials is a global leader in providing high-technology material solutions. The Advanced Materials' portfolio includes silicone-based products and technology platforms, silanes, fused quartz, ceramics, sealants and adhesives. These material solutions are used as a catalyst for innovation in hundreds of consumer and industrial applications ranging from car engines to biomedical devices. Markets served include aerospace, agriculture, appliances, automotive, construction, electronics, furniture and furnishings, healthcare, home care, industrial, lighting, packaging, personal care, plastics, semiconductor, telecommunications, tire, transportation, and water purification. As a Worldwide Partner of the Olympic Games, GE is the exclusive provider of a wide range of innovative products and services that are integral to a successful Games. Experience more at geadvancedmaterials.com.
*VaporStar, Metallist, Classic, and StabilizerPlus are trademarks of General Electric Company.
Contacts
The Americas
Monica Ettamarna
GE - Advanced Materials,
Strongsville, Ohio
Tel: +1-440-878-5740
E-Mail: monica.ettamarna@ge.com