Regal Introduces Turnkey Retrofits of Live-roller Conveyor for Energy Efficient, Low-maintenance Performance
Share:
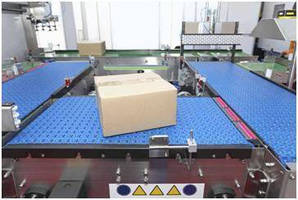
PROMAT Show News
Regal Booth No. 968
Retrofits bring safety and sustainability advantages with new plastic chain or belt, premium-efficiency reducers, and long-lived, sealed bearings.
Conveyor surfaces engineered for bottles, cartons, cases, people – even cars.
FLORENCE, KY  – Regal Power Transmission Solutions is introducing at Promat a new turnkey retrofit program that transforms live-roller conveyor for sustainable, high-uptime performance. Combining its System Plast® modular plastic belt and chain, high-efficiency Hub City or Grove Gear drives and long-lived Sealmaster® material handling bearings, Regal provides single-source or à la carte capabilities for on-site evaluation, consulting, layout design, validation and installation. The variety of conveying surfaces available from System Plast creates new options for every material handling need from single bottles to cases, people and even cars.
"Live-roller conveyor is old technology that has many weaknesses compared to recent advances in plastic chain and belt," said Mike Suter, Vice President for Regal Power Transmission Solutions. "Live-roller is noisy with pinch points from day one, and gradually turns into a downtime and maintenance problem with dead zones, belt wear, tracking and replacement, and complex snub roller center drives. Converting a system makes economical use of existing conveyor frame, while the new solution reduces product damage, part count, maintenance, downtime, noise, and energy consumption."
Promat highlights System Plast roller-top and heavy-duty belt
System Plast engineers a wide variety of conveyor belt and chain for low-maintenance, high-efficiency performance, utilizing proprietary polymer formulations to suit application requirements. Demonstrating its flexibility at Promat, Regal will demonstrate its directionally unlimited roller top belt that can align products to any angle, divert them, sort to multiple lanes, rotate, combine, or gap them – all done softly without contact. System Plast 2253RT roller top belt simplifies conveyor design and installation with its independently controlled moving surface that easily handles large or small, flat-bottom products, moving them on half-inch (12.5 mm) balls spaced on one inch (25.4 mm) centers. It supports loads up to 617 lb/ft (9,000 Nm/m) or 1.1 lb/ball (0.5 kg/ball). The belt's non-contact product manipulation eliminates impact and abrasion damage from pushers, as well as the need for mechanical adjustment or changeovers for conventional diverters or guides.
System Plast heavy duty and extra heavy duty plastic belts provide a non-skid, energy efficient conveyor surface for moving walkways, automotive assembly lines, car washes, and general material handling of heavy loads, such as barrels, drums, kegs and pallets. In Regal’s experience, these are the strongest and toughest 2" (50.8) pitch belts in the industry, and currently used on automotive assembly lines in Europe. The belts handle loads up to 5,400 lb/ft and 7,800 lb/ft (80 kN/m and 115 kN/m) respectively. Both styles are ideal for moving assembly line floors where the belt's non-skid, solid surface protects against slips and prevents tools and small parts from being trapped. The belts' unique design allows pusher bars to be attached, removed or replaced by the user at any time without disassembly of the belt, using molded-in drilling locators. Both belts utilize a patent-pending retention clip for the hinge pin. It can be installed or removed from either side of the belt with simple tools, as well as re-used. The molded-in non-skid surface of hexagonal dimples is ideal for people movers, offering a high coefficient of slip resistance under oily or dry conditions.
HERA® 90-percent efficient gear reducer
Hub City High Efficiency Right Angle (HERA®) reducers are the 21st century replacement of industrial worm-gear drives, providing 90% efficiency in all ratios for up to 40% reduction in energy requirements. Torque-dense with double the capacity of worm drives, HERA drives reduce motor size requirements, as well as the physical size of the drive package. HERA reducers save up to $550 per year with each increment of motor horsepower for rapid payback, and they are warranted for three years. Wide torque capacity and modular shaft, base and flange components allow just four sizes of HERA reducers to interchange with worm reducers from 1.75" (44.45 mm) to 6" (152.4 mm) center distance, reducing inventory requirements. Maximum torque ratings for the four sizes are 1,100, 2,600, 4,500 and 8,500 in-lbs (124 Nm to 960 Nm). The smallest and largest HERA reducers are available in stainless steel, and packaged drives with Marathon or LEESON motors are available as well.
Lightweight aluminum gear reducers
Grove Gear Bravo gear reducers feature a lightweight, single-piece aluminum housing that is vent-free and protected with high-temperature nitrile output seals. Bravo reducers weigh as much as two thirds less and are one-third smaller than cast-iron designs. Interchangeable with drives commonly found in material handling and packaging systems, Bravo reducers are designed for frequent reversing and start-stop cycles with oversized high-speed bearings and a bronze alloy worm gear centrifugally cast onto an iron hub for maximum strength and lubricity. IEC motor inputs and metric outputs make Bravo drives an excellent replacement for popular worldwide material handling reducers. Five sizes are available in ratings to 7.5 hp (5.6 kW) and ratios from 7:1 to 70:1, with center distances from 1.18" (29.9 mm) through 3.35" (85 mm). They are also available as integrated drives with Marathon or LEESON.
Sealmaster material handling mounted bearings
Sealmaster material handling bearings are designed with features to provide years of maintenance-free performance. Available in pillow block, tapped base pillow block, flanged and wide-slot take-up housings, all of them start with a solid cast iron base or housing for improved stability and resistance to shock and vibration. A standard contact nitrile rubber seal helps keep contamination out and facilitates grease purge, and an auxiliary flinger helps protect the seal from direct contamination. Both SKWEZLOC and setscrew locking styles are available, and optional snap-on end caps provide an extra level of personal protection from rotating shafts. Sealmaster's unique zone hardening of the inner race improves lock reliability by reducing distortion at setscrew locations.
For more detailed information on Regal Power Transmission Solutions products and services, visit www.RegalPTS.com
About Regal-Beloit
Regal-Beloit Corporation (NYSE:RBC) is a leading global manufacturer of innovative and efficient solutions for motion control, air flow and power generation. Headquartered in Beloit, Wisconsin, the company serves customers from its facilities located in the United States, Canada, Mexico, South America, Europe, South Africa, Asia and Asia Pacific. The company’s common stock is a component of the S P Mid Cap 400 Index and the Russell 2000 Index.
Contact:
Jackie Catalano
Director, Global Marketing Communications
Regal Power Transmission Solutions
Jackie.catalano@emerson.com
Tel: 859-727-5271
Release No. MCWR15004E
Â