DUDEK and BOCK: Instant Measurement Systems
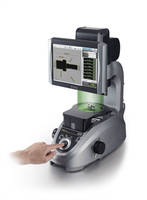
More than Quality
Inspection bottlenecks jeopardize on-time delivery and hurt the company's bottom-line, so how did Dudek and Bock Spring Manufacturing Company instantly solve their inspection problems?A visit from a key customer's engineering group is something that many in the contract manufacturing world dread; in some cases, however, that visit reaps great rewards for supplier and customer alike. This was recently the case with Chicago-based Dudek and Bock Spring Manufacturing Company, a leading supplier of metal products to the automotive, appliance, building construction, energy products, and virtually any industry that uses springs, stampings, wire forms, or assemblies.
One of Dudek and Bock's customers is a global provider of automotive seating solutions. The Tier 1 manufacturer works closely with its suppliers, not only to assure high quality products, but also in the role of continuous improvement (CI) support on the production floor. Vice-president of Quality Assurance Eipe Varghese became directly involved in one of these CI projects when it was discovered that machine tools were sitting idle for long periods of time during first-article inspection.
"The team was working on improving the changeover time on one of our wire forming lines," says Varghese. "This involved single minute exchange of die (SMED) and other Lean practices designed to make the line more efficient while also assuring continued part quality. The problem was that it was taking way too long to inspect the parts and provide the necessary dimensional feedback to the operator so he could make the correct machine adjustments."
The inspection process for this particular part is intense. The workpiece—a wire form for a headrest locking mechanism referred to by shop employees as "the zigzag part"—has dozens of complex angular, linear, and radial dimensions that were being measured on an optical comparator, each one requiring the time-consuming series of knob turning, crosshair alignment, and manual result recording most quality people are painfully familiar with.
"Each 30-piece sample was taking around 8 hours to measure," Varghese says. "If there was a problem, they'd have to go back and make adjustments, and then start the process over again. We knew there had to be a better way."
The customer's Global CI Director, who is typically more focused on production improvements rather than metrology, remembered seeing a digital comparator demonstration several years earlier at a spring and wire show in Dusseldorf, Germany. He suggested Varghese contact KEYENCE.
"They have an office nearby and were at our facility the next day," says Varghese. "Once we saw what the machine was capable of, we bought it on the spot."
The machine? KEYENCE's IM Series: A digital comparator that uses a high-resolution CMOS camera and intelligent pattern-matching algorithms to measure up to 99 dimensions on 100 different workpieces simultaneously. There's no need for fixtures or clamps—just set the part on the stage and push the measure button. Within seconds, the data is collated, analyzed, and the results displayed on the screen, recorded to a database, and can be printed out immediately for use on the shop floor.
Quality Manager Casey Luberda was the lead on the new piece of equipment. Luberda jumped right in with the new system, and had the IM largely mastered within a few days. "It's pretty simple to operate," he says. "The person that does the training for KEYENCE in this area has been back several times since, and on each visit shows me little tricks I can do to make my life easier. They've been very good to work with."
Luberda now writes all the programs for the IM and has trained others how to operate it. Compared to an optical comparator, he says it takes roughly one-fourth the time to layout a new part, and "around fifteen seconds" to measure once the program is done. Oftentimes, however, he doesn't bother writing a program. "For down and dirty measurements, dimensional verifications and such, I find it's faster on the IM Series than on the mechanical comparator. You don't have to worry about positioning the part, you can just throw it up there and tell the computer to check from here to there and you're done."
The IM Series may make Luberda's life easier, but it's those on the shop floor who appreciate it the most. That's because the Dudek and Bock quality procedure mandates that two pieces be inspected every time a job is setup. Before the KEYENCE, this took an average of two hours to complete, during which the machine sat idle.
"If we've run the job before, they're in and out of here in a few minutes," Luberda says. "The other cool thing is that, even if I'm in the middle of a program or something, it's easy to break in and check a dimension for one of the operators. I don't even have to write a report; I just hand him the printout with the results. The IM's a huge timesaver for all of us. I love it."
www.keyence.com/DudekAndBock
KEYENCE has steadily grown since 1974 to become an innovative leader in the development and manufacturing of automation equipment worldwide. Our products consist of automation sensors, static eliminators, barcode readers, measuring instruments, vision systems, laser markers, and digital microscopes.
Keyence Corporation of America
1100 North Arlington Heights Rd. Suite 210, Itasca, IL 60143
Phone: 1-888-KEYENCE (539-3623)
Fax: 1-201-930-0099
marketing@keyence.com