Production Test: Monitoring a Metal Stamping Press
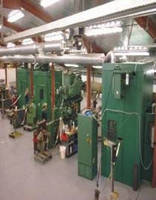
ADwin-Light-16 Real Time Data Acquisition System
CHESTERLAND OH - CAS DataLoggers recently provided the real-time data acquisition solution for an automotive manufacturer using metal stamping presses to shape their torque converters. Stamping was used to create a series of indentations that held metal vanes used to transmit the power from the engine to the transmission though a fluid. Hydraulic cylinders were used to force a hardened punch into the metal which was displaced into a corresponding die, creating 136 separate indentations. However, the punches, being extremely hard, were occasionally subject to breakage. In this automated environment, where one part was turned out every 45 seconds, many defective parts could be fabricated before an operator's visual inspection detected that the indentations weren't properly formed and that a punch had failed. Since the plant ran 3 simultaneous punching operations, failures sometimes occurred as often as once per shift, leading to a great deal of scrap since the parts couldn't be reworked. Therefore plant management looked for a highly accurate data acquisition and control device which could continually monitor the stampers' punches in real time for signs of developing breakage. An advanced DSP and user-friendly software were system necessities.
The automotive manufacturer installed a custom system designed by CAS DataLoggers incorporating an ADwin-Light-16 real-time data acquisition and control system to measure the force generated during the stamping operation. A load cell was attached to each hydraulic cylinder used to drive the individual punches, providing highly-accurate feedback from the punch's force. Appropriate signal conditioning was used to amplify the low-level signal from the load cells to a -10 to +10 volt signal for the ADwin system. A load cell signal conditioner provided excitation and amplified the low-level signal from the load cells, while a signal from the PLC used to control the press was fed into the ADwin's event input to trigger the acquisition cycle. The force waveform was sampled at 1 kHz over the period during which the part was stamped, including all 136 separate indentations. The ADwin immediately computed the maximum and minimum force and compared it to a pre-defined window for each. If the value fell outside that window, the ADwin sent a signal to the PLC through OPTO-22 signal isolators (providing isolation and TTL-to-line voltage conversion from the ADwin to the PLC) to indicate that there was a problem.
This 16-channel data acquisition system featured 8 16-Bit analog inputs, 2 16-Bit analog outputs, and 6 digital inputs and outputs (TTL/CMOS compatible). The system also utilized a local 32-Bit SHARC DSP with its own local memory to handle system management, data acquisition, on-line processing and control of outputs. Several configurations were available to choose from including PCI, CompactPCI, and EURO USB configurations, or external USB or Ethernet.
Real-time development was performed using the included ADbasic software. With ADbasic, users easily optimized and compiled the program code, and the real-time processes executed independently after being loaded on the system. ADbasic's functionality gave access to all inputs and outputs as well as functions for floating-point operations, process control and communication with a PC. A library complete with standard functions including filtering, various examples for counter use, closed-loop controllers, and function generators made for a quick implementation.
The automotive manufacturer benefited significantly following installation of the custom ADwin-Light-16 data acquisition and control system to provide real-time monitoring of their stamping operations. Use of the ADwin system allowed the plant's broken punches to be detected immediately, greatly reducing scrap costs and wasted time, and as more data was collected it became easy to identify tooling that had become worn prior to failure, which further reduced scrap and machine downtime. The early-warning system also reduced the once-constant need for operators to inspect each part for defects. The ADwin system formed an economical solution, and the included ADbasic software enabled programming of mathematical operations and functions which were executed immediately after each sampling step.
For more information on the ADwin-Light-16 real-time data acquisition system, additional sophisticated equipment from Jager, or to find the ideal solution for your application-specific needs, contact a CAS Data Logger Applications Specialist at (800) 956-4437 or visit the website at www.DataLoggerInc.com.
Contact Information:
CAS DataLoggers, Inc.
12628 Chillicothe Road
Chesterland, Ohio 44026
(440) 729-2570
(800) 956-4437
sales@dataloggerinc.com
http://www.dataloggerinc.com