This article is sponsored by CJWinter, a custom solutions provider for your material forming needs.
Pitch diameter — also called effective diameter — is the imaginary halfway mark of a thread form. It is based solely on thread features, thread groove, minor diameter with the thread crest, or major diameter. Pitch diameter can be found at the point where thread groove width and thread crest width equal one another, and are equal to half the thread’s nominal pitch.
Centerless Grinding for Thread Rolling
One of the most important steps in the thread rolling process for high precision threads is centerless grinding of pre-rolled thread diameter (pitch diameter). The centerless grinding process allows the correct pitch diameter to be developed before rolling the thread, working to control its diameter within 0.0004 inches (10 microns). This grinding process delivers a diameter that already features excellent surface finish before the thread rolling process.
Thread rolling can be used for any ductile metal. It is a cold forging process that is used to deliver special forms. For best quality, centerless grinding should be conducted using precision centerless ground blanks. Rolled threads deliver high shear, fatigue, and tensile strength.
Accurate Gauging
A thread needs to be rolled until its pitch diameter is within specification between maximum pitch diameter and minimum pitch diameter. Carefully crafted precision designs for blanks and thread rolling designs make the thread rolling process more efficient.
During the thread rolling process, any material that lies below the thread’s pitch diameter will be displaced through cold forming. Excess material will be squeezed into the thread’s new major diameter. Because no material is taken off the thread during the rolling process, the inherent weaknesses associated with cut threads or ground threads are eliminated. Pitch diameter measurements can be made over pins, or by using pitch micrometers.
When thread rolling occurs close to the thread’s major diameter, use the following ratio: For every 0.001-inch adjustment to blank diameter, the major diameter of the thread will be changed by 0.003 inches.
Pitch Diameter Inspection
Pitch diameter inspections should be done with full-form and single-element indicator gauges as determined by thread masters. Inspecting major diameters is done with standard outside diameter micrometers. Inspection of minor diameters and root radii is performed using optical comparators.
Blank size before roll threading should be near the maximum pitch diameter. Material displaced during roll threading by the dies used will form up, falling within the tolerance of the major diameter. Variables such as die wear can impact the thread rolling process. When machines are set according to these specifications, the thread rolling process delivers repeatable consistency.
To achieve accurate diameters, threads need to be rolled to the point where pitch diameter falls between the specified minimum and maximum pitch diameters. Centerless grinding offers a method to create accurate pitch diameters prior to thread rolling and limits the need for additional finishing processes, driving efficiency and repeatability throughout the thread fabrication process.
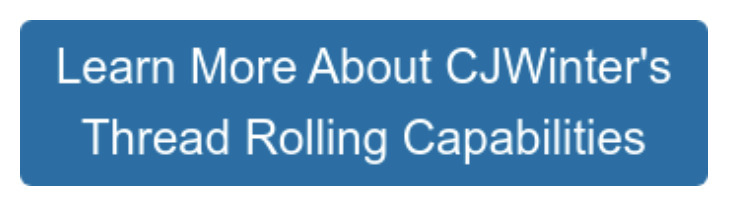